写真 さて、水性ニスにするか、油性ニスにするか考え中のDIY女子
しかしまぁ〜何ですなあ~。
コロナウイルスで世界中は大混乱。
東京オリンピックは延期が決定されたし。
このコロナウイルスは人為的に作られたウイルスに間違い無いだろう。
この手のウイルスを作ろうと思えばある程度バイオの知識がある人なら、その気になれば自宅でも出来る。
まあ要するに、幾つかのウイルスの遺伝子を組み替えて新しいウイルスを作ればいいのだ。いろんなウイルスを作れば、中には物凄く危険性のあるウイルスが出来上がる可能性もある。
と言う事で、一年くらい経てばこのコロナ事件は収まるとは思うが、第二、第三のコロナウイルスが世界に蔓延すると思う。模倣犯と言うやつか。
まあ、その時はその時だ。どんな時や!?
当記事では、昨年2019年に自作した超重量級オーディオラックにニスを塗って仕上げたので、その作業過程を紹介したい。
では、本題に入ろう。
製作費約一万円で出来る超重量級オーディオラック
今から約一年前の平成31年2019年4月30日(火)にワテが作成したのが、以下の記事で紹介している超重量級オーディオラックだ。ちなみにこの日は平成年号最後の日で、翌5月1日(水)から令和元年が始まったのだ。
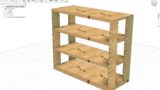
ホームセンターでサブロク板(1820x910x12)針葉樹合板を7枚カットして貰って、木工用ボンドで貼り合わせるだけで完成するにもかかわらず、物凄く丈夫なオーディオラックなのだ。
上で紹介した記事に、その製作過程を詳しく解説しているが、ここでは簡単に振り返ってみよう。
超重量級オーディオラックの設計図
Autodesk社の3次元CADのFusion360を使って設計した。
下写真では、四本の支柱で支える構造に設計したが、実際に作成したのは側板を平面構造に変更した。
下図に示すように、内寸で幅1028x奥行450x高さ260の棚が3段あるので、大型オーディオ機器を合計6台収納可能だ。
棚板には12ミリ厚の針葉樹合板を三枚貼り合わせて作成した36ミリ厚の板材を使ったので、物凄く頑丈なオーディオラックが完成した。
中央部分に支柱を入れていないが、それにもかかわらず60キロ弱の体重のワテが棚板の上に乗っても殆ど撓まない。
上図では棚板二枚版だが、当記事を執筆した時点でもう一枚棚板を作成して追加した。その製作過程も以下で紹介する。
超重量級オーディオラックの木取り図
まあ、ワテと同じオーディオラックを自作してみたい人は、下図を印刷してホームセンターや木工所に行ってサブロク板をカットして貰えば良い。
合計7枚の針葉樹合板を使う。
サブロク板(1820x910x12)
JAS規格 ホルムアルデヒド発散等級 F☆☆☆☆)
価格1000~1500円くらい
- 針葉樹合板が7枚(1300円x7=9100円)
- カット料金 ワンカット20円x20回くらい=400円
- 木工用ボンド 500円
超重量級オーディオラックの製作過程
ホームセンターでカットして貰った針葉樹合板を下写真に示す。
合計7枚の針葉樹合板をカットして貰うので、上写真はその一部だ。針葉樹合板は一枚約10キロくらいあるので7枚だと70キロ前後。
あとは、木工用ボンドとクランプを使って貼り合わせるだけだ。
ワテの場合には、木工用ボンドだけで貼り合わせた。釘や木ネジは一本も使っていない。
その理由は、将来、例えば表面を鉋掛けしたいとか、あるいは、どこかに追加工して穴を開けるなどする時に、釘や木ネジなどの金属類があると刃が欠けるなどの危険性があるからだ。
それに、木工用ボンドで接着すると物凄く強固に貼り付くので、釘や木ネジなどを併用しなくても、木工用ボンドだけで十分な接合強度を実現出来るのだ。
金属製接合金具(ジョイント)は極力使わない主義
ワテの場合、木工作業においては極力金属製のジョイント部品などは使わない主義だ。
例えばアマゾンで2x4材用の金属製接合金具を見るとこんなに沢山ある。
良く使われるのが2x4材向けのジョイント金具だ(下写真)。

或いは木ダボで接合する方式もDIYでは良く使われている。

まあこの手の手法は、ワテは殆ど採用しない。
その理由は、そんな便利なものに頼りたくないからだ。ワテの場合、木組みだけで組み立てる事を理想としているのだが、現状ではそこまでは無理なので木工用ボンドを併用する事で妥協している。
それに、素人DIYの製作例を見ていると、安易にこの手のジョイントを使って家具を作っているのを良く見かける。ワテの場合、自称DIYの達人なので、世間の凡人が採用する手法なんて決して使いたくないのだ。
つまりまあ、飛鳥時代に法隆寺を作った宮大工さんの心境だ。ほんまかいなw
と言う事で、ワテは今後、益々木工技術を磨いていつかは各種の伝統的な日本の継手技術を習得したいと思っている。
例えば、
- 婆沙羅継ぎ(大坂城大手門)
- 四方鎌継ぎ
- 兜巾(ときん)組み
などだ。
その時には宮大工ワレコと呼んでくれ!
棚板の固定方法はワテ独自考案の大入れ組手モドキ
下写真のように棚板は側板に形成した凹の部分に食い込んでいるので、棚板に重量物を載せても棚が落ちる心配はない。
このような組手を木工の世界では大入れ継ぎとか大入れ組手と言うのだが、本来なら側板に溝彫り加工が必要になる。
でも電動工具(ルーターとかトリマー)を使えば溝彫り加工は可能だが、ワテの場合はそんなツールは持っていない。
そこで、側板に小板を立ててその上に棚板を載せるアイデアで大入れ継ぎ風の構造を実現しているのだ。
組み立て時には、ゴムハンマーで叩いて組み立てるだけで完成する。
下写真のように大入れ継ぎが完璧に決まっている!
天板と側板の接合部分は、段々になるように加工してみた。
上写真では段々にした継手部分に1ミリくらいの隙間が出来てしまった。
ホームセンターの木材カットの加工精度は、お店の木工担当者さんの腕前にもよるが、一般的に±2ミリくらいの誤差はある。なので、もしカット後の木材の寸法が設計よりも数ミリ長い場合には、事前に鉋(かんな)やサンダーなどで削って寸法を設計値通りにしてから組み立てると良い。
ここまでが、昨年2019年4月に自作した超重量級オーディオラックなのだ。その後、このオーディオラックは、オーディオ機器だけでなく部屋にあるガラクタなど色々載せていたので、オーディオラック本来の使い方をしていなかった。
つまりまあ、単なる整理棚になっていたのだ。
ニスを塗って仕上げる
さて2020年3月に部屋を整理整頓しているのだが、不用品は捨てて部屋を掃除すると同時に、オーディオラックも本格活用する事にした。
まずはニスを塗って仕上げる事にする。
ワテの場合、大昔に買ったブラックアンドデッカー社のオービタルサンダーを持っているのだが、壊れて上手く動かない。
電源オンするとモーターは回転するのだが、ヤスリ面が振動しないのだ。ヤスリ面を部材に強く押しあてると、時々は振動を始めるが、非常に不安定。それと、振動し始めると物凄く大きな振動が手に伝わって来るので、まともに作業が出来ない。
サンダーの電源スイッチを切るのが困難になるくらいの大きな振動で、両手で支えないと手から飛んで行くんじゃないかと思うくらい大きな振動の勢いなのだ。
分解修理も検討したのだが、ここは思い切って新しいサンダーを買う事にした。
マキタ仕上サンダM931を買った
ワテが買ったのはマキタ仕上サンダM931だ。
仕上げサンダと言う商品名だが、所謂、オービタルサンダー(研磨面が長方形で偏心運動する)だ。
写真 マキタ仕上サンダM931の箱
ワテが買ったのは前者のM931だ。
なお、後者のBO3701はM931とは色が異なるが、中身は殆ど同じらしいので安い方を買うのが良いだろう。どちらもDIY用なので、業務用ではない。
もし仕事で毎日何時間も研磨するような用途には、本格的なプロ用のサンダがお勧めだ(下写真)。
さて、ワテの場合には、休みの日に偶に日曜大工をする程度なのでDIY用で十分だ。
写真 マキタ仕上サンダM931の箱を開封
下写真がマキタ仕上サンダM931の本体と付属品一式だ。
写真 マキタ仕上サンダM931本体、紙やすり(60番、240番各2枚、ダストバッグ、取扱説明書)
マキタ仕上サンダM931の仕様
回転数:11000回転/分
電源:100V
電流:2.0A
コード:2m
標準付属品:ダストバッグ、サンディングペーパー(粒度60・120・240各2枚)
使い方は簡単で、長方形のサンディングペーパーをサンダー底面に置いて、前後にある金属レバーを外してからサンディングペーパーを折り返して挟み込めば良い。
写真 マキタ仕上サンダM931の拡大写真
上写真で、台座の前後に二本のシルバーの金属棒があるのが見えるだろう。
例えば右側(後部)の金属棒には黒色プラスチックツマミがあるのが見える。その黒色ツマミを少し押し下げて左に動かすと金属棒の固定(クランプ)を解除できる。そうすると、数ミリの隙間が開くのでその隙間にサンディングペーパーを折り返して挿し込む。そして再び黒色ツマミを固定金具に引っ掛ければ完了だ。
その操作を、前後二カ所で行う事でサンディングペーパーをサンダーの台座に固定出来る。
サンディングペーパーのサイズは93×228mmなので、マキタ純正でも良いし、市販の互換品でも良い。あるいは、普通の紙ヤスリを買って来て自分で93×228mmサイズにカットし使っても良いだろう。
ペーパーに開いている穴は削りカスを吸塵する為の物だ。M931の場合集塵バッグ付きなので、使い易い。あるいは電動集塵機のパイプを挿し込めば、より強力に吸塵する事が出来る。
上写真のやつはマキタ製ではないが、サイズ約23 x 9.5cm(L x W)なので、マキタ93×228mmとほぼ同じだから問題無く使えるだろう。そして安い。
オービタルサンダー(研磨面が長方形)とランダムオービットサンダー(研磨面が円形)
さて、サンダーには幾つかの種類がある。ここでは代表的な三種類のサンダーを紹介しよう。
オービタルサンダー(研磨面が長方形)
ワテの場合、この長方形研磨面は単純に前後運動をしていると思っていたのだが、違うらしい。
前後運動では無くて回転運動なのだ。長方形の研磨面が半径数ミリくらいの円運動をしている。
このような動きを偏心運動を言う。
オービタル(Orbital)とは楕円運動と言う意味だ。
その結果効率良く研磨できる。
ただし、この次に紹介する研磨面が円形のランダムオービットサンダーのような大きな回転運動ではないので、大きく削りたい用途には向いていない。
どちらかと言うと仕上げ研磨と言う感じ。
なのでマキタM931も「仕上サンダ」と言う名前が付いているのだろう。
ランダムオービットサンダー(研磨面が円形)
ランダムオービットサンダーとかランダムアクションサンダーと呼ばれるタイプのサンダーがこれだ。
研磨面が円形だが、グラインダーのような単純な回転運動ではない。
研磨面は回転運動すると同時に円の中心軸が、偏心運動するのだ。
先ほど紹介した長方形台座のオービタルサンダーは偏心運動のみであったが、ランダムオービットサンダーは偏心運動と同時に研磨面が大きく円運動しているのだ。
つまりまあ、偏心運動する長方形台座のオービタルサンダーの研磨面がクルクル回転しているイメージだ。
となると、円形台座のランダムオービットサンダーの研磨効果は、長方形台座のオービタルサンダーよりもかなり高い。
従って、部材の凸凹を手っ取り早く研磨して平滑化したい場合には、この円形台座のランダムオービットサンダーがお勧めだ。
逆に言うと、削り過ぎる危険性もある。
例えば、車のボディにコンパウンド入りのワックスを塗って、バフを付けてこの手のランダムオービットサンダーで研磨すると物凄く効率良く研磨できてピカピカになる。
ボディの平坦部分ならそれでも良いが、ボディのデザイン的なエッジ部分にサンダーを強く押しあてて研磨すると、エッジ部分が集中的に研磨されるので磨きすぎて下地の板金が露出する場合もあるので要注意だ。
ちなみにBOSCH社のランダムオービットサンダーは冒頭に挙げたBOSCH 吸じんランダムアクションサンダー PEX260AE以外に以下の二つも有名だ。
何が違うのか気になったので、以前、ボッシュさんのお客様相談室に電話して聞いてみた。その結果、詳しく教えて貰ったのだが、ワテの記憶が確かなら以下のような主旨の説明だった。
商品写真 | 商品名 | ワテがBOSCHさんに教えて貰った内容 |
![]() ![]() |
BOSCH(ボッシュ) 吸じんランダムアクションサンダー PEX260AE 電動サンダー コンパクト 低振動 研磨 |
DIY用 目安としては週一回くらいの頻度で使う人向け |
![]() ![]() |
Bosch Professional(ボッシュ) 吸じんランダムアクションサンダー+ポリッシングスポンジセット GEX125-1AEJ2 |
セミプロ用 上や下の製品の中間くらいの使用頻度の人向け。プロの人にはお勧めしない。 |
![]() ![]() |
BOSCH(ボッシュ) 吸じんランダムアクションサンダー GEX125AVE |
プロ用 日常的に仕事で使う人向け |
表 BOSCH社のランダムアクションサンダーの主要三製品のお勧めユーザー
あくまでワテの記憶に基づいて書いた説明なので、気になる人はボッシュさんに聞いてください。
確かに三番目のプロ用のやつは値段も高い。
ベルトサンダー(研磨面が帯状のベルト)
ワテの場合、この手のハンド型ベルトサンダは使った事は無いのだが、物凄く良く削れるのかな?
上で紹介した長方形台座のオービットサンダーや円形台座のランダムオービタルサンダーはどのメーカーの製品でも消費電力は200W前後が多い。
一方、上のマキタベルトサンダは650Wもある。本格的なプロ用のベルトサンダだと1000W級もあるのだ。
兎に角、物凄く良く削れるのだろう。
あるいは、下写真のような小型のベルトサンダを一台持っていると、込み入ったパーツの研磨に威力を発する。
例えばYouTube動画で見たのだが、バイクのエンジンの空冷フィンなどの狭い場所を研磨してエンジンをレストアする場合にこの手のハンド式小型ベルトサンダーが使い易そう。
あるいは据置型の本格的なベルトサンダーもワテも一台欲しいなあと思っている(下写真)。
リョービのこの製品は有名だ。中華製の似た様なコピー商品が多数出回っているようだが、本家オリジナルはこのリョービ製品なのかな?
針葉樹合板で作ったオーディオラックの棚板を一枚追加する
製作過程の写真は撮っていないのだが、オーディオラックの棚板を一枚自作して増やす事にした。
いつものようにホームセンターで針葉樹合板(サブロク板を二枚)をカットして貰った。
寸法1052x450x12の板を三枚作る。
それを木工用ボンドで貼り合わせてクランプで固定して一晩乾かせば完了だ。
既に製作済の棚板二枚と、新たに作成した棚板一枚の合計三枚を屋外に持ち出した。
棚板は12ミリ厚の針葉樹合板を三枚重ねで貼り合わせているので、木口には1ミリ程度の凹凸がある。
その段差をマキタオービタルサンダーM931を使って平坦に削るのが目的だ。
三枚の棚板を重ねて四隅を四つのF型クランプで固定する。
棚板は一枚36ミリ厚なので三枚だと10cmくらいの厚さだ。
その四辺の木口をマキタオービタルサンダーM931を使って綺麗に研磨した。
さらに、棚板のエッジはホームセンターのパネルソーで切断したままの鋭いエッジなので、その部分もサンダーで面取りして平滑化した。
最後に、棚板の表面(見える部分)もサンダーで軽く磨いておいた。
この手の作業は屋外でやるのに越した事は無い。吸塵器を付けて研磨クズを吸い取ったとしても、やはり多少の木くずが飛散するからだ。
針葉樹合板で作ったオーディオラック棚板に油性ニスを塗る
まずはホームセンターで水性ニスを買って来た。
ワテが選んだのはアサヒペンの水性アクリルニス透明だ。
セールで安かったので(30%オフ)。
あとは70ミリ幅刷毛で塗ってみた。
3月下旬だが天気も良くて晴天だったので、乾きも早い。
でも、乾いた表面をみると期待していたほどは光沢が無い。
油性ニスならもっと光沢が出るのかな?
それとも水性ニスでも重ね塗りすれば光沢が出るのかな?
ワテの場合、塗装の経験はそんなには豊富ではないので良く分からない。それでも自称DIYの達人だw。
で、水性ニスを乾かしている間に、同じホームセンターに再び行って油性ニスを買って来た。これも安売りしていたのでw。安売りに弱いワテである。
先ほど水性ニス(クリアー)を塗った棚板に油性ニス(ゴールデンオーク)を塗ってみた。その結果、わりと光沢のある皮膜が出来た。
あとで分ったのだが、光沢の皮膜が出来るかどうかは水性塗料や油性塗料の違いではなくて、塗り重ねる回数のようだ。
一回目の塗装の場合、塗料は木肌に染み込むので光沢が出にくい。なので二回、三回と重ね塗りをすれば光沢は出るのだ。特に今回使った水性アクリルニスや油性ウレタンニスのようにアクリルとかウレタンなどの樹脂成分が入っている塗料なら重ね塗りをすれば光沢は出るのだ。
重ね塗りの場合の注意事項としては、綺麗に仕上げるには、塗って乾いたら240番くらいのペーパーで研磨する。そして次の塗装を行うのが良いだろう。
で、兎に角、三枚の棚板にアサヒペン油性ウレタンニス(ゴールデンオーク)を塗った。
その写真はこの後で紹介する。
超重量級オーディオラックの本体に油性ウレタンニスを塗る
さて、超重量級オーディオラックはその名の通り超重量級だ。全体で50~60キロくらいの重量だと思うが計測していない。
棚板一枚でも5~6キロあると思う。
ラックの本体の写真を下に示す。一枚数キロの板を四角に組んでいるので、20キロくらいかな。
写真 オーディオラックの本体に油性ウレタンニスを塗る準備
まあ20キロもあるし、部屋から外に持ち出すのは重労働なので断念した。
なので、上写真のように床には新聞紙を敷いて部屋の中で塗装する事にした。
塗りにくい箇所から塗るのが塗装の基本
素人の人はついつい塗り易い箇所から塗ってしまう。
本棚なら下写真の天板の広々としたところに塗ってしまう。でもそれは失敗の元だ。
写真 塗装の基本は塗りにくい場所を先に塗る
天板を先に塗って綺麗に仕上げたとしても、その後で側面のエッジ(上写真)を塗ったとすると、天板部分にまで余分な塗料がはみ出してしまい、折角綺麗に仕上げている天板に塗装斑(むら)が生じるのだ。
なので、上写真のように先に側面の塗り辛い箇所を塗るのだ。自称DIYの達人だ。まあそんな程度の知識は誰でも知っているかw
さて、合板の木口部分の塗装が完了したので、次はいよいよ天板部分に油性ウレタンニス(ゴールデンオーク)を塗っている(下写真)。
写真 オーディオラックの天板部分にアサヒペン油性着色ウレタンニス(ゴールデンオーク)を塗る
ホームセンターで安売りしていたニスは、他にも、ウォールナット、ダークオークなど濃い目の色もあったのだが、ワテの場合は薄い色合いのゴールデンオークを選んだのだ。
なお、上写真において、合板三枚重ねの天板の木口が今一つ綺麗に仕上がっていない理由は、木口をサンダーで研磨していないから。
棚板は屋外に持ち出して、木口をサンダーで研磨したのだが、ラック本体は部屋の中から出せなかったのでサンダー研磨は断念した。ただし、角の部分だけはハンド式のヤスリ(下写真)で面取りして手触りを良くしている。削ると同時に掃除機で木くずを吸い取った。
このタジマのハンドサンダーは半永久的に使えるのでお買い得だ。
底板表面にもアサヒペン油性着色ウレタンニスを塗る
底板にもニスを塗った。
まずは両端の塗り辛い箇所に塗る。また前後のエッジの部分にも塗る。
写真 オーディオラックの底板にも油性着色ウレタンニス(ゴールデンオーク)を塗る
油性ウレタンニス(ゴールデンオーク)を塗り終えたコーナー部分
写真 油性ウレタンニス(ゴールデンオーク)を塗り終えたコーナー部分
やはり、木口をサンダーで研磨していないので仕上がりが今一つ綺麗ではない。
でもまあ、ラックとしての機能性には影響ないので気にしないw
人間、細かい事は気にしないのが一番だ。
と言うワテは、物凄く細かい事が気になるww
棚板の塗装失敗例
下写真はアサヒペン油性ウレタンニス(ゴールデンオーク)を塗装した後、棚板を立て掛けて乾燥させていたのだが、節の窪みに溜まった塗料が流れ落ちてしまった。
写真 節に溜まった塗料が流れ落ちた失敗例
まあ、十分乾燥して固まったら紙やすりなどで磨くかな。
あるいはオーディオ機器を載せれば見えないから、このままでもいいかな。
兎に角、先に進もう。
考える暇があれば手を動かすのがDIYの基本だ。
オーディオラックの塗装が終わったので組み上げる
アサヒペン油性ウレタンニスの場合、冬場の乾燥時間の目安は3時間から6時間くらいだ。
まあ2時間くらいしか経っていないが、ほぼ乾燥したので組み立ててみる。
写真 オーディオラックの下段棚板を設置した
上写真のように、側板は12ミリ合板を二枚貼り合わせている。その内側に棚板を支える小板を立て掛けて、その上に棚板を載せると言う簡単な構造だ。
この構造をワレコ式大入れ組手と呼んでいる。
棚板支え小板は単に立て掛けているだけなので不安定な気がする人もいると思うが、実際には、重量5キロくらいの棚板が乗るので勝手に小板が倒れる心配はない。
棚板の取り付けはゴムハンマーで行う
棚板の横幅は実測でも設計通り1052ミリに仕上がっている。
一方、棚本体の口の字型の枠の内寸は設計では同じく1052ミリなのだが、実物は数ミリ狭いのだ。
その理由は、天板、底板の寸法は設計通りなのだが、口の字に組み立てた時に口の左右の側板が内側に少し撓んでいるのだ。
図解するなら、
側板形状は本来┃ ┃のように平行になるべきだが、実際は極端に書けば )( こんな感じ。
その結果、棚板を載せ辛い。
その対策としては、ゴムハンマーで側板を外側に叩くと、上手い具合に棚板は自重で落ち込んで行く(下写真)。
写真 棚板の取り付け時に、側板がキツイ場合にはゴムハンマーで側板を広げる方向に叩く
注意事項としては、側板を叩くのでは無くて直接に棚板を下方向に叩いて嵌め込むのはお勧めでは無い。
まあその方法でも棚板は取り付けられるが、棚板を直接叩いてしまうと棚板木口が側板に擦れるので棚板木口に横方向の摩擦が加わり、その結果、木口が裂けてしまうのだ。
なので、棚板を叩き付けるのでは無くて、側板を広げる方向に叩くのが良い。
自称DIYの達人のアドバイスだ。と言うかワテも最初は棚板を叩いてしまい、失敗したのだw。
達人にも失敗はある。
無事に塗装が完了したワレコ式の超重量級オーディオラック
無事に完成した超重量級オーディオラックを写真で紹介しよう。
写真 無事に塗装が完了したワレコ式の超重量級オーディオラック全体写真
上写真において、ズームレンズで撮影しているので写真の上部が極端に広がっているが、実物は設計図の寸法プラスマイナス1ミリくらいの精度で組み立て出来ている。
なお、最上部の二枚の側面小板は取り付けなくてもオーディオラックの棚板の機能性には影響しないのだが、見た目の観点でこの部分にも側板小板を取り付ける事にした。
でも塗装するのを忘れていたw
まあ、時間が有る時に塗るかな。
アサヒペン油性ウレタンニスの缶入り0.7リットルを買ったのだが、上写真のオーディオラックを塗装しても、まだ底に3cmくらいは残っている。これだけ有れば側板二枚の塗装には足りそうだ。
二回塗りした棚板は光沢が出た
一度目はアサヒペン水性アクリルニス(透明)を塗った棚板三枚であるが、二回目はアサヒペン油性着色ウレタンニス(ゴールデンオーク)を塗った。
その結果、分厚い皮膜が形成されて、光沢がある綺麗な仕上がりになった。
写真 二度塗りしたので分厚い皮膜が形成出来たオーディオラック棚板
上写真のように、棚板は側板に取り付けた小板の上に乗っているので、M8クラスの地震でも来ない限り自然に倒れる事は無いだろう。
と言う事で、ワレコ式の合板貼り合わせ方式による大入れ組手モドキの方法によって、だれでも手軽に本格的なオーディオラックを作成出来るのだ。完璧だ。
最上部の側面小板の塗装を忘れていたw
まあそれは気にせずに、ワレコ式の超重量級オーディオラックの細部をご覧ください。
天板はアサヒペン油性着色ウレタンニス(ゴールデンオーク)一回塗りなので光沢も少ない。ツヤツヤした光沢を出すにはやはり重ね塗りが必要だ。
写真 ワレコ式の超重量級オーディオラックの最上部棚板写真
棚板のみ水性アクリルニスの上に油性着色ウレタンニス(ゴールデンオーク)を重ね塗りしているので、まるで漆塗りの高級家具のような仕上がりだ。
ほんまかいなw
写真 高級山中塗の漆塗り製品に勝るとも劣らない油性着色ウレタンニスの仕上がり?
まあ、ワレコ式の超重量級オーディオラックも遠くから見れば高級な山中塗に見えなくはない。
ワレコ式の超重量級オーディオラックの堂々の完成
と言う事で、最上部の側板の塗り忘れはあるが、完璧な塗装が完了した。
その結果、ワレコ式の超重量級オーディオラックは棚板も一枚追加して4段式となり、手持ちのオーディオ機器は全部載せられる。
棚板間隔は実測で上から下に155/159/159/260だ。
設計では、上三段は均等な間隔になるはずだったのだが、何故か155/159/159になってしまった。理由は不明だ。まあいいw
もちろん棚板支え小板の寸法を自由に変更出来るので、どんな棚板間隔にも簡単に変更出来る。
また棚板枚数も幾らでも変更出来る。
このようにワレコ式超重量級オーディオラックは他に類を見ない完璧な設計なのだ。オーディオラック史上の金字塔と言っても過言ではない。ほんまかいなw
ワテの場合、リサイクルショップで買ったやっすいPA用のパワーアンプを持っているのだが、重さ30キロくらいあるが、この自作オーディオラックならビクともしない頑丈さだ。
それにもかかわらず費用総額1万円(木材)+塗料3千円(二回塗り)で完成する。
なお、普通の家具(箪笥、食器棚など)なら家具の台座の部分がある。
所謂、袴(ハカマ)と呼ばれる部分だ。
ワテ自作のラックには現状では台座も脚も何も無いが、数センチの厚みのハカマを自作してその上にラックを載せる予定だ。
そのほうがラック最下部(底板)が床から10cmくらい離れるので、見た目が美しいかなと思うので。
オーディオラックの袴を作成した
その後、2x4材が余っていたのでオーディオラックの袴(ハカマ)と呼ばれる台座を作成した。
家具のハカマは台輪(だいわ)とも呼ばれる。口の字に組んだ木枠を床に敷いて、その上に家具を載せて支える台木だ。家具と一体になっているタイプもある。
さて、ワテの場合にはHiKOKIの卓上スライド丸ノコFC7FSBを持っているので傾斜カットも自由自在に出来る!
HiKOKI 卓上スライド丸のこ FC7FSBの場合、最大45度の傾斜カットが可能だ。
取付穴径:20mm
最大切断寸法(mm):(90°)高さ59×幅305・(左傾斜45°)高さ35×幅240
テーブル角度切断範囲:左45°~右57°
傾斜切断範囲:左45°~右5°
電流(A):11
回転数:6,000min-1
HiKOKI 卓上スライド丸のこ FC7FSBの主な仕様
かつ、ワテの場合には、90刃の超仕上ハイパーチップソーを使っている。
まあ、FC7FSB標準装備の日立工機純正72刃でも切れ味は悪くは無いのだが、ネットで評判の高いこのSK11ハイパーチップソー90刃を買ってみたのだ。使った感想は、物凄く良く斬れるし、切断面も綺麗だ。
FC7FSBの傾斜カットで材木位置の調整方法
傾斜カットの場合、刃が木材のどの位置を切り込むのか分かり辛い。
FC7FSBの場合には、45度カットの場合には、下写真に示すように下部回転台座(ターンベース)にある青色樹脂部分の左端から20ミリの位置に丸ノコ刃が切り込む(ワテの実測)。
なお、注意事項としては、上写真のように金属製のスケールなどをスライド丸ノコのターンベースに載せるのは非常に危険だ。うっかりこのまま丸ノコを使ってしまうと大事故が起こり得る。
実際、ワテもこの写真撮影の直後にうっかり上写真のままスライド丸ノコを使ってしまうところだったが、直前で気づいた。桑原桑原w
万一の事故を想定して、この手の用途に使う定規は金属製ではなくて樹脂製や竹製が良いだろう。100均で竹製物差しを一本買っておく予定だ。
スライド丸ノコを使うと斜めカットも自由自在
スライド丸ノコを買って正解だった。
下写真に示すように斜めカットが正確に出来る。
もしこの手の斜めカットを手鋸でやるとなると、かなりの熟練した大工さんでない限り、難しいだろう。
あるいは、単純な電動丸ノコを使って45度斜めカットをする場合には、直線に沿って滑らせるためのガイドが必要になる。
専用の作業場が有ればその手の作業は出来なくは無いが、ワテみたいに狭い工作室しかない人には、スライド丸ノコは本当に素晴らしい電動工具なのだ。
スライド丸ノコは見た目は何か大掛かりな工具に見えるが、実際に使ってみると設置場所も1メートル四方くらいの場所が有れば良い。工具自体は固定状態で使うので、電動丸ノコみたいに工具を動かすツールと比較しても、スライド丸ノコは使い易いのだ。
もし2x4材などの2メートルくらいの部材をカットしたい場合にはスライド丸ノコの左側に2メートル程度の空きスペースが必要になる。
ワテの場合には、大型部材のカットの際には、スライド丸ノコを広い場所に移動してカットしている。スライド丸ノコは重量もそんなには重くないので、必要ならいつでも動かせるのだ。
スライド丸ノコで短い部材をカットする場合のテクニック
短い部材をカットしたい場合には、付属のクランプでは押さえられないので、下写真に示すようにF型クランプを使って木材をアルミ台座に固定すると良い。
ただし、スライド丸ノコのスイッチを入れて前後に動かして切断する前に、スイッチは切った状態で事前に丸ノコの移動をシミュレーションしておく必要がある。
つまり、F型クランプにスライド丸ノコのどこかの部分が当たってスライド丸ノコを前後移動出来ないなどの問題があるからだ。
あるいは、最悪の場合、丸ノコ刃がF型クランプの金属部分に接触すれば大事故が起こるので、事前にそのような問題が出ない事を十分に確認したあとで、本番のカットを行うようにする事。
かつ、安全メガネは必須だ。
安全メガネならミドリ安全、3M、山本光学の製品が有名だ。
ラック袴の部材のカットが完了したので接着剤で組み立てる
下写真に示すように、コーナークランプを使って袴の四つの部材を木工用ボンドで貼り合わせた。
ワテが使っているのは以下の製品だが、一個千円ちょいなので8個だと一万円弱。
最近では、以下のような4個セットも安く売っているのでお買い得だ。
ただし、この手の工具はたまにしか使わないけれど、使う時には正しく機能してくれないと物凄く気分が悪い。なので「安かろう悪かろう」な工具はお勧めしない。ある程度はレビュー評価が高い商品を買うのが良いだろう。
具体的には、この手のクランプの場合、安いやつだと薄い金属で作られているので、強く締め付けると歪んでしまって直角が出ないなんてのもあるようだ。いくら安いと言ってもそんな工具は使いたくない。
と言う事でワテの場合には、冒頭で紹介した緑色のSK11(エスケー11) コーナークランプ 固定板幅 70mm以下 SKC-1を8個買ったのだ。使った感想としては、機能的には満足しているが、回転軸に付いている金属棒が数センチと短いので、強く締め付けると手が痛いw
まあ気にしない。
ラック袴のコーナー部分を補強する
45度カットが簡単に出来るので、四つの補強部材を即席で作成した。
それらをF型クランプを使ってコーナーに木工用ボンドで貼り付ける。
袴の製作においても、木工用ボンドだけで組み立てた。釘は一本も使っていない。まさに法隆寺を建てた宮大工さんの心境だ。
無事に完成したので、アサヒペン水性アクリルニス(ゴールデンオーク)を塗った(写真撮影忘れた)。
次に、袴が床に接触する部分に保護の目的で、カーペットを帯状にカットして接着剤で貼り付けた。
上写真の白いのが安い切り売りカーペットを帯状に切ったものだ。
カーペットの表面(繊維面)が床に接触するようにしている。なのでカーペットの裏面に接着剤を塗って袴に貼っている。
袴に載せたワテ自作の超重量級オーディオラックの完成写真
写真 袴に載せたワテ自作の超重量級オーディオラック
どう!いい感じでしょ。
袴が無い場合と比べて、袴の上に載せるとキリッと締った感じがする。
その袴の拡大写真を以下に示す。
写真 アサヒペン水性アクリルニス(ゴールデンオーク)を塗ったオーディオラック
上写真において、袴はホームセンターで売っている2x4の杉材を使った。ニスを塗る前に本当ならサンダーで研磨しておくと塗装が綺麗に仕上がるのだが、今回は手抜きして何もせずにニスを塗った。
その結果、袴の表面が多少荒いがまあ機能的には問題無いので気にしない。
なお、ニス塗りを忘れていた最上部の二枚の側板にもニスを塗ろと思っていたのだが、又しても忘れてしまった。
自称DIYの達人のワテもボケて来たのかw
あかんがな。
まとめ

ワレコ
当記事では、ワテが2019年4月に自作した超重量級オーディオラックに、2020年3月に塗装を施した過程を紹介した。
ホームセンターで売っている安い針葉樹合板(サブロク板1820x910x12)を7枚カットして貰って木工用ボンドで貼り合わせるだけで完成するにも係わらず、本格的な木工で採用される大入れ組手構造を実現しているので、棚板一段辺り100キロくらいの機材を載せても棚板が落ちる心配はない。
製作費用は約1万3千円。
内訳は以下の通り。
項目 | 単価 | 数量 | 小計 |
針葉樹合板(1820x910x12) | 1300円 | 7枚 | 9100円 |
カット料金 | ワンカット20円 | 30回 | 600円 |
ニス(0.7リットル) | 1500円 | 1缶 | 1500円 |
刷毛70ミリ | 100円 | 1本 | 100円 |
合計 | 13300円 |
表 ワレコ式の超重量級オーディオラック(塗装費用含む)の費用内訳
まあ綺麗に仕上げたい人は、塗装前にサンダーで研磨すると良いだろう。
ワテならサンディングペーパーの100、240、400番辺りを順番に使って表面研磨しておくかな。
その後で、水性ウレタンニスを塗る。
乾燥したら400番の耐水ペーパーをサンダーに付けて表面研磨。
これを3回繰り返して三回塗りすればツルツルの光沢のある綺麗なオーディオラックが完成するだろう。
今回は、作業環境の問題もあり、そこまでは完成度の高い塗装は出来なかったが、それでも一回塗り(棚板は二回塗り)にも係わらず、上写真で紹介したようにメーカー製高級オーディオラックに勝るとも劣らない完成度の物が出来た(と言う事にしておく)。
今回は水性アクリルニス、油性着色ウレタンニスの二種類を使ったが、今後は水性塗料のみにするかな。油性塗料は匂いが臭いので部屋の中で使うと数日間は臭い。それと油性塗料は使用後の刷毛や容器の手入れが面倒だ。
ペイントうすめ液やシンナー、灯油などで洗うなど必要だが、出来ればやりたくない。刷毛は一本100円程度で買えるが、それでも使い捨ては気が引ける。
そう言う点では、水性塗料なら匂いも少ないし、使用後の手入れは水洗いで可能なのだ。刷毛も何度も再利用出来るので、ある程度品質の良い高級刷毛を使う事も可能だ(下写真)。
この世の中にこんな高級刷毛があるのか!
自称DIY達人のワテも知らなんだ。
まあなんと言っても、今回紹介したワレコ式の超重量級オーディオラックは、ワテ考案の側面小板支え方式の大入れ継ぎ構造を採用しているので、手軽に製作出来るにもかかわらず100キロ級のオーディオ機器を棚板に載せてもビクともしないのだ。
費用総額1万円ちょい。
皆さんにもお勧めしたい。
DIYや日曜大工は楽しい。
都心のタワマンなんて何が良いのか分からない。
災害が有ればエレベーターが止まるし。そもそもタワマンなんかに住んでいたら日曜大工すらできないだろう。週末は自宅ガレージでDIYが男のロマンだ!
今では女性でもDIYをやる人は多いらしいし。
郊外の一戸建て住宅なら、完成したオーディオ機器(自作アンプ、自作スピーカーなど)を大音量で鳴らしても近隣から苦情も出ないし。
コメント