
ワレコ
スピーカーを自作する事にした。
オーラトーン風の小型密閉キュービックスタイルにしてみる。
では本題に入ろう。
ワテが今までスピーカーを自作しなかった理由
ワテの場合、オーディオ機器(アンプ、DACなど)の自作は好きなのだが本格的なスピーカーを自作した経験は無い。
その理由を説明しよう。
スピーカーの自作はボックスを作ってスピーカーユニットを取り付けるだけで良いから、木工作業としては簡単だと思う。
もちろん、装飾性や見栄えにこだわったボックスを作る場合には木工のテクニックも必要だが、単に音を出すと言う目的なら箱だけ作れば良いから難易度は低い。
しかしながら、スピーカーの音は完成してみない事には分からない。
時間を掛けて完成度の高い木製エンクロージャーを製作したとしても、スピーカーユニットを取り付けていざ音を聴いてみたら期待したような音が出ないなんて事は普通に有り得るだろう。
スピーカーの音は見た目では分からない
結局のところ、そのスピーカーユニットに最適なエンクロージャーを見付けるには、事前にシミュレーションするなどしてある程度は予測出来るとは思うが、最終的には実機を何個も作成して試行錯誤で最適なエンクロージャーを見つけ出すしか無いだろう。
具体的には、エンクロージャーの種類(密閉、バスレフ、ホーンなど)、寸法、容積、使う板材の厚さ、材質などだ。
オーディオメーカーのスピーカー開発部門なら、そう言う試行錯誤で何台もエンクロージャーを作ってみて試聴して、最適なエンクロージャーを完成させる事は可能だ。
しかし、個人でそんな試行錯誤は無理がある。失敗作のエンクロージャーを溜め込んでいても無駄だし、捨てるのも勿体ないし、再利用するとしても木工用ボンドで強固に貼り付けてしまったら分解し辛いし。
と言う訳で、エンクロージャーの製作は木工作業としては簡単だと思うのだが、出て来る音が期待通りになるとは限らないから、ワテはスピーカーの自作にはあまり興味は無いのだ。
ただし、市販の有名スピーカーを真似してレプリカみたいなのを安い予算で作る人もいるが、そう言うDIYに関しては、出て来る音もある程度は予測できるのでそう言うDIYは悪くはないと思う。
あるいは既に誰かが作成したスピーカーが評判が良ければ、それを真似して作るのも成功する確率は上がるだろう。例えば長岡式とか。
以上のような理由でワテは自分で独自に設計したスピーカーの製作はやった事が無い。大昔に中古ユニットを使って小さなスピーカーを作った事はあるが。
自分好みのスピーカーを買う方法
スピーカーを買うなら、ヨドバシカメラなどの大手オーディオショップに行って多数のスピーカーを試聴できる環境を利用して、実機を試聴するのが良いだろう。
自分の好きなCDを何枚か持参して、気に入ったスピーカーをとっかえひっかえ聴いてみれば良いのだ。
そんなふうにしてスピーカーを選ぶと失敗する可能性は低くなる。
同じスピーカーでも、お店の広々としたオーディオルームで聴くのと、自宅の狭い部屋で聴くのとでは出て来る音は必ずしも一致しない。
でもそのスピーカー自体はお店で聴いた音を出す能力が有る訳だから、あとは自宅でスピーカー設置環境を工夫すれば自分の好きな音に近づけることは出来る。
具体的には、スピーカースタンドの種類とか、高さとか、左右スピーカーの間隔とか向き、天井や壁の吸音材、その他スピーカーの音を決める要因は多数あるので、いろいろ試行錯誤して理想的な音になるようにすれば良いのだ。
Auratone風の密閉キューブ型スピーカーを自作する
そんなワテがスピーカーを自作する事にしたのだ。
使うユニットはCORAL 4F-1Bフルレンジだ。
大昔にリサイクルショップで見付けて自作スピーカーでも作ろうと思って買ったまま忘れていたのだ。
CORAL 4F-1Bフルレンジユニットを使う
その写真を以下に示す。
写真 純正箱入り未使用コーラル4F-1Bペア
これを物置で発見したのだ。
その中身は以下の通り。
写真 ウレタンエッジが加水分解してボロボロに劣化したコーラル4F-1B
上写真のようにウレタンエッジが加水分解してボロボロに劣化して破れている。
それを自分で修理したのだ。
ゴム製エッジを貼ってコーラル4F-1Bを修理した記事はこちら↴
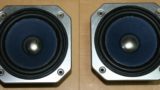
より詳しいエッジ交換方法の解説はこちら↴

下写真に無事にエッジ交換修理が完了したコーラル4F-1Bフルレンジ10cmスピーカーを示す。
写真 ゴム製エッジに交換したコーラル4F-1Bフルレンジスピーカー8Ω/50W全面
なかなか綺麗に貼れているでしょ!
写真 ゴム製エッジに交換したコーラル4F-1Bフルレンジスピーカー8Ω/50W背面
まあスピーカーは積極的には自作はしないワテではあるが、このコーラル4F-1Bを使って自作スピーカーを作る事にした。
当初はヤフオクあたりで売り払う事も検討したが、落札相場を見ても三千円とかで、高くても五千円くらい。
まあそれなら自分で活用してみようと思ったのだ。それに、ワテの木工作業環境は着々と使い易くなって来ているので、完成度の高いエンクロージャーを作る事も可能だ(ワテの能力次第で)。
Auratone風の密閉キューブ型スピーカーを自作する
ワテが日常的にPCオーディオ環境で使ってるスピーカーはAURATONE 5C SUPER SOUND CUBEだ(下写真)。
写真 AURATONE 5C SUPER SOUND CUBE
オーラトーンは1970年くらいの発売で、世界中のレコーディングスタジオや放送局などで使われている有名スピーカーだ。
コーン型フルレンジユニット(コーン紙Φ8cm、エッジ外周Φ10cmワテ実測)を密閉型の小さなエンクロージャーに取り付けている。
こんな小さい箱にスピーカーを取り付けると良い音が出ないんじゃ無いかと思うが、実際に聴いてみると人の声が聞きやすいのだ。
オーラトーン5Cは以下の点でワテのお気に入りだ。
- 人の音声が聞き取り易い(ニュース、ボーカルなど)
- 近距離で音声・音楽を聴いても違和感がない(ニアフィールドモニター)
- 小型立方体で重量もあるので安定性も良く、置き場所を選ばない
などである。
まあ要するにニアフィールドモニターとしてAuratone 5Cは有名なので、低音は出ない。あくまで人間の音声周波数帯域が聴き取り易いスピーカーなのだ。
もし低音をバンバン出したい人は、他のスピーカーを選ぶか、あるいはAuratone 5Cと別のウーハーを組み合わせて使うなどが良いだろう。
なお、PCオーディオで使うスピーカーは、Radiko、ラジル、YouTubeなどで人の声を聴く事も多いので、Auratone 5Cのような低音が出ないスピーカーは非常に都合が良い。人の声が聴き取り易いので。
もしそれを30cmウーハーを持つような3Way大型スピーカーなどに置き換えると、音楽再生には良いが人の声は低音が強調され過ぎて聞き取り辛いだろう。
そう言う点でも、Auratone 5C + サブウーハーと言う組み合わせで設置して、音声を聴くならAuratone 5Cのみ、音楽を聴くならサブウーハーを有効化すると言った使い分けが良いだろう。
あるいはAuratone 5Cのみを使ってアンプのラウドネスをONして低音を強調しても良い。
Auratone 5Cは今でもヤフオクで程度の良い物でも1万円前後で取引されているので、これからPCオーディオ用スピーカーを買う人にはお勧めしたい。
あるいは新品もある。
二台ペアで五万円弱だ。
CORAL 4F-1B用の密閉エンクロージャー製作
さて、そんな有名なAuratone 5C風の密閉型エンクロージャーを作ってCORAL 4F-1Bを入れてみる事にした。
使うのは針葉樹合板の端材とホームセンターで買って来たべニア化粧合板の端材だ。
エンクロージャーのサイズは、以下の通り。
ワテ自作 高185 x 幅185 x 奥230 mm
ワテ自作機のサイズは適当に決めた。
事前に何らかのスピーカー設計ソフトなどを使ってシミュレーションを行うなどもしていない。
奥行はAuratone 5Cの135mmに比べてワテ自作機は230mmと長いが、まあこれは長めにして容積を大きくしておけば、実際に試聴して吸音材の量など調整して容積を調整出来るので、大き目にしたのだ。
最初からエンクロージャーの奥行を短く切り詰めると、あとで伸ばす事は困難なので。
密閉・バスレフ・バックロードホーンのワテの印象
そもそもコーラル 4F-1Bを密閉小型ボックスに入れて良い音が出ると言う保証もない。通常ならバスレフタイプのボックスを作って、低音域もバスレフの効果で若干強調して使うのが普通だろう。
でもワテの場合は、バスレフ方式のスピーカーの音は今一つ好きでは無いのだ。
まあバスレフポートを使えば低音が増強出来るのは原理的には理解できるが、前から出る直接音と、背面からバスレフポートを通って来た低音とが時間差で合成されるわけだから、原理的にも見た目にも不自然な印象を受ける。
それなら密閉箱に入れて単発で鳴らす方がシンプルだし分かりやすい。
ちなみにワテはバックロードホーンも好きでは無い。
大昔に中古スピーカーユニットを使ってバックロードホーン風のスピーカーを自作した事があるが、低音がバックロードホーンを通って増強される独特の力強さを感じるが、何か違和感があった。
人工的にモワーっと低音を増強するような感じに聞こえた。その音は初めて聴くと新鮮な印象を受けるが、毎日聴いていると違和感を感じる(ワテの場合)。
音の速度は毎秒340メートルなので、3.4メートルのホーンなら0.01秒の時間差が発生する。34cmなら0.001秒の時間差が発生する。百分の一秒程度の時間差なら、敏感な人なら気付くだろう。
まあバックロードホーンの悪口を書くと長岡式マニアの人には怒られそうなので、これくらいにしておこう。
エンクロージャー製作開始
針葉樹合板の端材 約200x200x12が数枚有ったので、それを使った。
下写真のように185mm位置に木片を固定してストッパーにする。
写真 185mm位置にストッパーを固定して針葉樹合板12ミリ厚をカットする
上写真のようにして板材を卓上スライド丸ノコでカットすると、同じ寸法185mmに複数の板材をカット出来る。
この板を四枚作った。側板(185x185x12)になる。
縦185x横185の正方形箱型に組む為に、天板と底板は針葉樹合板二枚分の厚さ24ミリを引いた185-24=161mmでカットしたい(185x161x12)。
その為には下写真のように12ミリ幅針葉樹合板の端材を二本使ってカットするのだ。
写真 最初に決めた185mmストッパーは動かさずに161mm幅にカットするテクニック
上写真のように、最初にセットした185mm位置のストッパーは動かさないので、切断の精度が高まるのだ。
木工DIY素人の人はここでストッパー位置を161mmに変更してしまうのだ(昔のワテ)。
側板左右 185x185x12 二枚
天板、底板 185x161x12 二枚
の四枚の板を筒状に貼り合わせた(下写真)。
写真 左右側板と天板・底板を木工用ボンドで接合する(上部板はクランプ押さえ用)
この後、数時間放置して無事に接合出来た。
前面バッフル板の製作
前面バッフル板は、針葉樹合板12ミリに化粧ベニア5.5ミリ厚端材を木工用ボンドで貼る事にした(下写真)。
写真 針葉樹合板12ミリ厚と化粧ベニア5.5ミリ厚の端材をバッフル板に使う
下写真のように木工用ボンドを詰め替え袋で買って、100均容器に入れている。
写真 100均容器に入れた木工用ボンドをシリコン刷毛で塗ると使い易い
そのほうが節約できるので。
ワテが使っているシリコン刷毛は調理用のやつだ。
木工用ボンドの塗布はヘラを使う人も多いが、ヘラだと均一な厚みに塗布する事が難しい。
それに比べて刷毛で塗ると必要量を必要な場所に塗布する事が出来るのだ。
かつ、シリコン製の刷毛なので抜け毛も無いし、使い終わったら水洗いすれば綺麗に木工用ボンドを洗い流せる。
もし洗うのを忘れてボンドが固まってしまった場合には、一晩くらい水に漬けておけばボンドが水でふやけて白っぽく柔らかくなるので、あとは手でボンドを除去すれば良い。
写真 シリコン刷毛で木工用ボンドを均一に塗布した(ワテの木工DIYテクニック!)
上写真のようにシリコン刷毛で木工用ボンドを塗ると均一に塗れるのだ。
あとは下写真のようにクランプで圧着して乾燥させる。
写真 貼り合わせた針葉樹合板と化粧ベニアをクランプで圧接する様子
下写真のように、針葉樹合板12ミリと化粧ベニア5.5ミリを木工用ボンドで貼り合わせた。
写真 針葉樹合板12ミリと化粧ベニア5.5ミリを木工用ボンドで貼り合わせた
貼り合わせたバッフル板をカットするのだが、四隅から木工用ボンドが少し食み出していて凸凹している。
その状態だと卓上スライド丸ノコのガイドに突き当てても若干不安定だったので、ワテ自作の直線カット作業テーブルを使って丸鋸で切断した(下写真)。
写真 ワテ自作の直線カット機構付き作業台でカットしている様子
写真 ワテ自作直線カット機構付き作業台では端1ミリ幅でさえも正確にカット出来るのだ
上写真のように、端1ミリ程の部分を切り落とした。なお、切断開始直後に化粧ベニアが少しめくれてしまった。
まあこのベニアは印刷した安っぽい化粧ベニアなので、化粧面が剥げやすい。もし見た目が悪くなった場合には、改めて何か別の天然木材の突板(ツキ板)でも張るかな。
残りの三辺は卓上スライド丸のこでカットした。
前面バッフル板にスピーカー取り付け穴を開ける準備
スピーカー取り付け穴をこのバッフル板に開ける。
直径はコーラル4F-1Bスピーカーユニットの実測でΦ106ミリにした。
写真 捨て板(針葉樹合板端材)を敷いてその上に化粧面を下向きにしてクランプ固定
先ほどの丸ノコ切断で分ったように、この化粧ベニアは剥がれ易い。
そこで上写真のように針葉樹合板端材を捨て板として敷いてその上に化粧面を下向きにしてクランプ固定した。
マキタの電子ドリルを使って穴開け加工を行う。
写真 マキタ(Makita) 低速用ドリル 鉄工13mm 木工38mm 6304LRを使う(フレンチクリート収納)
ワテが使うのはマキタの電気ドリルだ。
速度可変、正転・反転切り替え、木工38ミリの大トルクなので使い易い。
- 電圧:単相交流100V
- 電流:7.5A
- 消費電力:710W
- 回転数:0~600(回転/分)
- 穴あけ能力:鉄工Φ13mm、木工Φ38mm
- ドリルチャック能力:Φ2~13mm
- 全長:358mm
- 質量:2.6kg
穴開けに使うのは自在錐だ(下写真)。
写真 マキタ6304LRドリルに取り付けたスターエム 自在錐 30×120、完璧な組み合わせだ
ワテは下写真の自在錐を持っている。今回はΦ106穴なのでΦ120まで対応している下製品で行ける。
もしΦ120以上の大穴を開けたい人は、別売りのロングバーに交換すればΦ300まで行ける。
なお、下写真の新型では、左右の刃の位置が連動して動くので目的の直径に合わせる作業がやり易い。
この手の自在錐は海外製のやっすいヤツも沢山あるが、まあワテの場合はスターエムさんのやつを買っている。
刃物で有名な兵庫県三木市にある1923年創業のドリルビット専業メーカーの株式会社スターエムさんの製品なので安心感があるのだ。
前面バッフル板に自在錐でΦ106を開けた
早速穴開け作業をやってみた。
写真 マキタ6304LRドリルとスターエム 自在錐 30×120で半分の深さ(約6mm)まで開けた
ワテの場合、ドリルの固定スタンドは持っていないので、フリーハンドで穴開け作業を行う。
本当なら下写真のようなマキタ純正ドリルスタンドが有れば良いのだが。
穴開け加工の途中で、ワテ自作のサイクロン集塵システムを使って切り屑を吸引清掃する。
写真 木工にはサイクロン集塵システムは必須だ
さて、半分まで穴開けしたら、板を裏返して反対側からも同じように穴開け加工をするのが自在錐の本来の使い方である。
でも、裏返すと化粧ベニア面なので、その面に穴開け加工をすると自在錐の刃で化粧ベニアが剥がれる可能性がある。
なので、裏返さずにそのまま穴開けを続けたら、難なく穴開けに成功した(下写真)。
写真 一気に17.5mm(12mm針葉樹合板+5.5化粧ベニア)にΦ106穴開け成功
下写真のように完璧な穴が開いた。
写真 自在錐使いの魔術師と呼ばれている超絶穴開けテクニックだ!
まあワテの場合、自在錐でスピーカー穴を開けたのは今回が初めての経験。
化粧ベニアが禿げたらどうしよう!とビビっていたのだが、やってみると案外簡単。
それにもし失敗しても、ホームセンターで買って来た一枚数十円の端材ベニア板だし。
そんなのに穴開けする前からビビってどうするw
超慎重派のワテである。
超小心者と同じやがなw
無事に穴開け加工が終わったので、下写真のようにサイクロン集塵ホースを使って床掃除。
写真 サイクロン集塵ホースを使って床の切り屑を掃除
このサイクロン集塵ホースはΦ50くらいの太めのやつなのだが、当初は少し太すぎたかなと思っていたが使ってみると、適度に重量もあり使い易い。
Φ32くらいの洗濯ホースなどを使う人もいるが、Φ50ホースなので吸引力も強い。
前面バッフル板をエンクロージャーに張り付ける
前面バッフル板に穴開け加工が終わったので、事前に筒状に組んでいた本体部分に木工用ボンドで貼り合わせた。
下写真にその完成形を示す。
写真 前面バッフル板(5.5化粧ベニア+12針葉樹合板)を針葉樹合板12ミリで組んだ本体に張り付けた
下写真のように背面は現時点ではまだ貼っていないので開放している。
写真 製作途中のエンクロージャーの背面
この時点でエンクロージャーの寸法は縦185x横185x奥218だ。
背面バッフル板の貼り付け
さて、下写真のように背面にも針葉樹合板12ミリを185×185の正方形にカットして貼り付けた。
写真 背面板(185x185x12)を木工用ボンドで貼り付けている様子
下写真に張り付けた背面板を示す。
写真 エンクロージャー背面に針葉樹合板12ミリを貼り付けて箱状になった
下写真のようにスピーカーエンクロージャーの形が出来上がって来たぞ。
写真 まるでくじ引きの箱のようなワテ自作のスピーカーボックス
う~ん、そっくりやw
仕上げサンダで表面を研磨する
正面は化粧ベニアを貼ったが、それ以外の面は針葉樹合板の素地のままだ。
素地の部分にはニスでも塗るか、あるいは、他の化粧板を張るかは未定だ。
取り敢えず、仕上げサンダで表面を研磨する。
写真 サイクロン集塵ホースに接続して研摩中のマキタ仕上げサンダ
当初は240番で研磨していたのだが、240番だと細か過ぎて大きな凹凸が削り切れない。
そこで60番の粗いやつに交換して研摩したら、段差も解消出来た。
なお、今回のエンクロージャー製作では、いつも以上に慎重に寸法を合わせて卓上スライド丸ノコでカットしたので、切断誤差は実測で0.2ミリ以下くらいに収まっている。
その結果、箱状に組んだエンクロージャーでも、接合箇所の段差は0.2ミリ以下だ。
なので、60番のペーパーを使うと数十秒で段差を研磨して除去出来た。
その後で、240番で仕上げしておいた。
下写真に研摩作業が終わったエンクロージャーを示す。
写真 仕上げサンダで表面研磨が完了したエンクロージャー
なお、上写真の左端に写っている切断端材は今回のエンクロージャー製作で発生したものだ。
ワテの場合、超貧乏性なので、これくらいの端材ですら捨てられない。
まあ溜め込んでおけば何かの役に立つし。
ガスケットを自作する
スピーカーユニットをエンクロージャーに嵌め込んで固定する時に、スピーカーユニットとエンクロージャーの間に挟むガスケット(パッキン)を自作する事にした。
下写真のようなやつだ。
近所のダイソーに行ったら厚さ5ミリのカラーボードと言うのを売っていた。素材は発泡ポリスチレンだ。
まあそれでも良かったのだが、5ミリはちと分厚い。一般的には2ミリ程度だろう。まあ柔らかいので5ミリでも圧縮すれば2ミリくらいにはなる。
何か他にガスケットに使えそうな素材をダイソーで探したら、手頃な素材が有ったので買ってみた(下写真)。
シリコーン鍋敷き(Disneyのミッキーマウス柄入り)だ。
写真 ダイソーのシリコーン鍋敷き(Disneyのミッキーマウス柄入り)をガスケットに加工する
下写真のようにシリコーン鍋敷きの中央に大きなミッキーマウス、周囲にも小さなミッキーマウスが円形に配置されている。
ミッキーマウスの部分は凹んでいるのでその部分は使いたくない。
サークルカッターを使ってミッキーマウス部分を外して円形に切り抜く。
下写真のようにΦ106で円形に切り抜く事が出来た。
Φ106円盤状になったシリコーン鍋敷きをエンクロージャーのΦ106穴に当ててみた(下写真)。
写真 エンクロージャーΦ106とピッタリ合ったシリコーン鍋敷きガスケットΦ106
そこにスピーカー(CORAL 4F-1B)を嵌めてみたらいい感じだ。
写真 エンクロージャーにガスケット(シリコーン鍋敷き)Φ106にスピーカーを嵌めた
あとは、下写真のようにはみ出す部分を切り取ってガスケットが完成した。
写真 ダイソー100円のシリコン鍋敷きで作成したスピーカーガスケット
シリコン鍋敷きは、カッティングボードの上でサークルカッターや普通のカッターで切り取れば簡単に加工できるのでお勧めだ。
ただし、シリコン素材がスピーカーのガスケットに適しているのかどうかは不明だ。
柔らかいEVA素材のガスケットならスピーカーの四隅を強固にネジ止めすると、ガスケットも適度に圧縮されてスピーカー金属フレームと木製エンクロージャーがかなり密接する。
一方、厚さ2ミリ程度のシリコーン鍋敷きを流用して製作したガスケットの場合、弾力性が強いので圧縮してもEVA素材ほどは薄くならない。
その結果、スピーカー金属フレームと木製エンクロージャーとの間に弾力性の高いシリコーンが挟まれる事になる。
そのシリコーンの弾性がスピーカーの再生音にどんな影響を与えるか?それは不明だ。
まあ、そんな事は気にせずにスピーカーの製作を続けよう。
兎に角、箱を作ってスピーカーを取り付けて、アンプを繋げば音が出るのだw
あとは上写真のような革用穴開けポンチΦ5を使ってガスケットの四隅に穴を開けた。
革ポンチなんて滅多に使わないが、DIYをやっていると時々だが小穴を開けたい場合がある。今回みたいに。
なので上写真のようなセットを買っておくといざという時に便利なのだ。
前面バッフル板に爪付きTナットを埋込む
さて、スピーカーの固定は四カ所のネジ穴で固定するのだが、当初は木ネジで固定する予定であった。
でもこれだと、何度もスピーカーユニットを取り外しているとネジ穴が馬鹿になるだろう。
かと言って、エンクロージャー背面も接着してしまったのでスピーカーユニットをボルトとナットで固定する事は出来ない。
そこで、前面バッフル板の裏側に爪付きナットを埋め込む事にした。
写真 爪付きTナットM4x8とM4六角穴付きキャップボルトでスピーカーユニットを固定する
ワテが採用したのが下写真のような爪付きナット(爪付きTナットとも呼ばれる)だ。
M4用の場合、Φ5穴を開ければ筒の部分を挿し込む事が出来る。
まずは下写真のようにボール盤を使ってΦ3の穴を四つ開けた。
そのΦ3穴四つを下写真のように慎重にΦ5に広げた。
下写真のようにバッフル板裏側から爪付きナットを嵌め込む。
そして、表側から下写真のようにM4のネジを嵌め込んで、インパクトドライバーで締め込むと爪付きナットが引き上げられて、四つの爪がバッフル板に食い込むのだ。
写真 バッフル板の化粧ベニアを養生しながらM4ネジを締めて爪付きナットを埋め込む
これで無事に爪付きナットを埋め込む事が出来た。
この後でスピーカーユニットを取り付けてM4キャップボルトを付けてみたが、爪付きナットの位置もピッタリと合っていたので、全てのネジ(左右8個)を完璧に固定する事が出来た。
オノカツさんのボルトは国産なので安心だ。
爪付きナット取り付けの注意事項としては、スピーカーフランジに開いている取り付け穴はΦ5くらいなので、爪付きナットの位置が1ミリでもずれるとボルトが真っ直ぐに入らないので、最悪、フランジ穴を削るなどの不細工な加工が必要になる。
なので、爪付きナットの取り付け穴は正確に位置を計測して開ける必要がある。
なお、爪付きナットに似たようなパーツに下写真の鬼目ナット(インサートナットとも言う)がある。
この鬼目ナットでもスピーカーユニットをボルト固定する事が可能だ。
ただし鬼目ナットをバッフル板に埋め込む為には、裏側(エンクロージャー内部)から鬼目ナットを挿し込んで、かつ、六角レンチを使って鬼目ナットを捻じ込む必要がある。
バッフル板あるいは背面板を貼り付ける前で有れば、鬼目ナットを取り付ける作業はやり易かったが、今回は背面板も貼ってしまったので鬼目ナットは取り付け辛い。
そこで爪付きナットを採用したのだ。
やはりワテくらいのDIY上級者になると、臨機応変に対応できるのだ。
ほんまかいなw
今日はここまで。
まとめ

ワレコ
取り敢えず箱状になったエンクロージャーにCORAL 4F-1Bを載せて、アンプに繋いで音を出してみた。
その結果、ワテの理想とするAuratone 5Cの音は出ていないw
まあ、内部に吸音材も入れていないし、左スピーカーのみで音出ししたし、スピーカーユニットを強固にボルト固定せずに載せただけだし、そんな状態で聴けば良い音は期待できない。
ただし、密閉箱に入れているので低音は控え目と言うか、ほとんど出ずに中低音から中音付近の音が良く聴こえた。
あとは兎に角完成させて、吸音材など幾つか試してワテの理想とする音にチューニングして近づけたい。
完成したら、ワテの布団サイドスピーカーとして使う予定なのだ。
今後の予定としてはスピーカー背面の端子取付作業だが、その部分の設計を工夫した。
詳細は次回の記事で紹介予定だが、普通のスピーカーターミナルだけでなく圧着端子やスピコンも接続可能な構造にするのだ。
必要なパーツはPCBWayさんに発注予定だ。PCBWayさんにはプリント基板だけでなく3Dプリンティング加工も発注する予定だ。
乞うご期待!
コメント