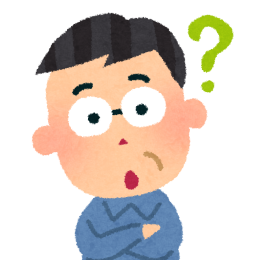
皆さん、
2024年パリオリンピック見てますか?
ワテは時々見ている。
さて、表題の「赤外線リモコン式 4入力オーディオセレクター ラッチリレー採用」がほぼ完成した。
8ビットマイコンATmega328Pや数個のロジックICを組み合わせたワテにとっては大掛かりな電子工作は今回が初めての経験だ。
PCBWayさんに発注していた専用基板が届いたので早速ハンダ付けしたのだ。
設計段階では正常に動くかどうか自信が無かったが、実際に作ってみると多少のトラブルは有ったが最終的には案外簡単にいい感じで動いた。
では、本題に入ろう。
前回記事はこちら⤵️
PCBWayに発注していた基板が到着
下写真にPCBWayさんからFedexで到着した小包を示す。
![]() |
![]() |
写真 FedexでPCBWayの小包が自宅に到着
今回PCBWayさんに発注したプリント基板は今まで何度も発注した中でも最速と言っても良いくらい速く届いた。
時系列でまとめると以下の通り。
今回の基板を発注 | 2024/7/17 11:40 |
追加発注1回目(同梱依頼) | 2024/7/17 19:29 |
追加発注2回目(同梱依頼) | 2024/7/17 20:58 |
Fedex発送 | 2024/7/20 05:45 |
自宅に到着 | 2024/7/23 |
つまり、7月17日の昼頃に今回のプロジェクト用の基板を発注し、その後、当プロジェクトとは別の基板の追加発注を2回行った。そして7月20日の早朝にはFedex発送され7月23日に到着したのだ。6日で届いた事になる。
速いわ。
ちなみに、追加発注した基板は最初に発注した基板と同梱して貰った。それらの手続きはPCBWayさんの基板発注画面で簡単に指定出来る。
![]() |
![]() |
写真 PCBWayの小包を開封
上写真の右に示す青色レジスト基板が今回使う基板だ。
その拡大写真を下に示す。
写真 今回PCBWayさんに発注したリモコン式ラッチリレー採用4chセレクター基板
この基板の仕様を以下の表にまとめてみた。
寸法 | 140 x 100 mm |
層 | 2 層 |
材質 | FR-4: TG150 |
板材の厚み | 1.6 mm |
レジスト | 青 |
シルク | 白 |
表面処理 | 有鉛はんだレベラー |
銅箔の厚み | 1 oz Cu(=35μm) |
要するにガラスエポキシ1.6mm厚の両面スルーホール基板だ。
こういう専用基板が6日で自宅に届くのだから、電子工作をやる人には嬉しい時代がやって来たもんだなあと染み染み思う。
なお、上写真では基板にPCBWayさんのロゴが入っているが、これはワテが基板をPCBWayさんに発注した事をメモする目的で入れている。自動的にPCBWayさんのロゴマークが入るのでは無い。
ちなみにKiCadを使うと基板には文字だけでなく、このように画像データも描ける。PCBWayさんのロゴも画像データで描いている。
基板の設計パラメータの紹介
初めて基板を設計する人は、例えば下写真の白い線や文字がどれくらいの大きさで描かれているのか気になるだろう。
写真 4つのラッチリレー取り付け部分の拡大写真
例えば上写真にある「U11、U12、R23、1K」などの文字は以下のパラメータで描いている。
幅 | 1 mm |
高さ | 1 mm |
太さ | 0.15 mm |
リレーの絵柄を描いている線分の幅は0.12mmだ。
PCBWayさんには過去に何度も基板を発注しているが、これくらい小さな文字や線も問題なく綺麗に印刷されて基板が出来上がる。過去には幅0.8mm, 高さ0.8mmの極小文字を入れた事もあるが、それも問題なく印字されていた。
この基板は表裏にベタアースを配置して、多数のVIA(表裏を電気的に接続する小穴)で連結している。例えば下写真左では基板上に小さな穴が多数あるがそれがVIAだ。写真右がKiCadの設計図で、手作業でランダムにVIAを配置している様子を示す。
![]() |
![]() |
写真 左:多数のVIAの例、右:KiCadのレイアウトデータ
このVIAの仕様は以下の通り。
ビア穴 | 0.3 mm |
ビア直径 | 0.6 mm |
要するにVIAと言うのはドリルでΦ0.3mmの小穴を開けて、そこにビア直径Φ0.6mmのリング状のパッドを付けてスルーホールのような形状にするのだ。ドリル径やビア直径は自由に変更出来る。
例えばビア穴Φ0.8mm、ビア直径1.6mmくらいの大きめのVIAを作ると、それは両面スルーホールのユニバーサル基板に空いているスルーホールと同じような見た目になる。
専用基板にパーツのハンダ付けを開始
今回発注した基板ではIC類はDIPタイプのものを採用し、抵抗・コンデンサ・ダイオードなどは表面実装部品(SMD)を採用している。
本当はICもDIPではなくてもっとコンパクトな表面実装型のフラットパッケージタイプを採用したかったのだが、それは断念した。
と言うのは、このプロジェクトはワテにとってはマイコンや幾つかのICを組み合わせた初めての本格的なデジタル機器の電子工作なので、上手く動くかどうかやってみないと分からない。
動作実験の試行錯誤の中でICを壊す可能性もあるので交換し易いようにDIP型ICをICソケットに挿せるように今回の基板を設計したのだ。
では、早速部品をハンダ付けする。
表面実装型3端子レギュレータをホットプレートでリフローハンダ付けする
今回使うラッチリレーは秋月電子で以前に買ったオレンジ色のやつで電源電圧は5Vだ。
また8ビットマイコンATmega328Pも動作電圧は5Vだ。
なので基板上に7805三端子レギュレータを搭載してDCジャックで供給する外部電圧(DC8~35V)から5Vを作り出すように設計した。
その三端子レギュレータは表面実装型なのでまずはそれを最初にハンダ付けする。
表面実装型の三端子レギュレータは手作業でのハンダ付けは難しいので、調理用の小型ホットプレートを利用してリフローを行う。
以下ではワテ流の手法を紹介するが、今まで十回以上このやり方でリフローしているが、失敗した事はない。
下写真の基板上のハンダメッキされた大きめの銀色正方形部分にSMDタイプの7805三端子レギュレータをハンダ付けするのだ。
写真 表面実装型の三端子レギュレータ7805をハンダ付けする場所
下写真のようにその正方形の電極部分と二つの足の部分にハンダごてを使って適量のハンダを盛っておく。
写真 正方形電極部分と二つの足の部分にハンダごてを使って適量のハンダを盛る
ハンダを盛ったらその上にフラックスを塗布してから下写真のように三端子レギュレータを載せる。
写真 ハンダを盛った上にフラックスを塗布して三端子レギュレータを載せる
これで準備完了だ。
一方、下写真のように小型ホットプレートの電源をONしてプレートを加熱する。
写真 小型ホットプレートの電源をONしてプレートを加熱
上写真でプレートの上に糸ハンダの小片を載せているのが分かるだろうか。
その拡大写真を下写真左に示す。プレートの温度がハンダの融点に達したら下写真右のようにハンダが溶けてボール状になる。
![]() |
![]() |
写真 ホットプレートの表面温度を調べるためにハンダ小片を載せるテクニック
ハンダ小片がボール状になったらプリント基板隅のネジ穴をラジオペンチで摘んで下写真のようにホットプレートの上に基板を載せる。
写真 プリント基板隅のネジ穴をラジオペンチで摘んでホットプレートの上に基板を載せる
下写真はホットプレートで加熱中の三端子レギュレータだ。
写真 ホットプレートで加熱中の三端子レギュレータ
今までの経験で言うと数分前後で事前に盛っておいたハンダが溶ける。今回は基板サイズが140x100mm2と大きめだったせいか、若干時間が掛かった気がするが正確には時間は計測していない。
兎に角、数分後にはハンダが溶けて三端子レギュレータが電極に密着するのを目視で確認したら、ラジオペンチを使って基板を持ち上げてダンボールを敷いた作業机の上に置いた(下写真)。
写真 ホットプレート加熱を終了してダンボールの上で冷却中の基板
ワテの場合は作業机の上にダンボールを敷いているのだが、ダンボールは電子工作に何かと便利だ。適度なクッション性もあるし今回のように熱にも強い。
汚れたり破れたりしたら交換も簡単。上写真のようにかなりボロボロになってきたので、そろそろ交換時期かも。
さて、ホットプレートを使った三端子レギュレータのリフローハンダ付けの出来具合を確認するために実体顕微鏡を使って観察した(下写真)。
写真 ホットプレートリフローしたハンダ付けの出来具合を実体顕微鏡で確認
上写真のようにまあまあいい感じにハンダ付け出来た。
今回はホットプレートリフローでハンダ付けしたのは三端子レギュレータ1個だけだったが、もちろん複数のデバイスを同時にリフローハンダ付けしても良い。
なお、ワテの手法ではハンダ小片がボール状になってから基板をホットプレートに載せた。
当初は室温状態のホットプレートに基板を載せてから電源ONしてリフローした事も有ったのだが、それでも問題なくリフローハンダ付けには成功したが、今はその手法はやめた。
なぜなら基板を載せたホットプレートを室温から徐々に加熱するとハンダの融点に達するまでに数分掛かる。その間も基板に載せた電子部品は加熱されているが、熱で部品を破壊する危険性を考えれば、融点に達してから基板を載せるほうが良いかなあと言う判断なのだ。そのほうが部品を加熱している時間は短くなるので。
その判断が正しいかどうかは不明だが、あくまで現在のワテはプレート表面がハンダ融点に達してから基板を載せるようにしている。
要するに茹で卵を作る場合に水を入れた鍋に卵も入れて沸騰させるか、水だけを入れた鍋を沸かして沸騰したら卵を入れるかの違いだ。どっちでも良いかも知れないが。
表面実装型のLEDを手ハンダ付けする
次は今回使う部品の中で最小の表面実装型LEDを手ハンダ付けする。
先ほど取り付けた5V電源を使って、電源ONの状態を示す為の緑LEDを点灯させる回路だ。下写真D2がそのLEDで、R2は電流制限抵抗。
写真 0805(2012M)サイズのLEDを手ハンダ付けする
さて、このLEDは秋月電子で売っているOptoSupply社の長さ2.0x幅1.25x高さ1.0mm (0805)と言う極小のLEDだ(下図)。
図 OptoSupply社の緑LED(OSXX0805C1C)2.0×1.25×1.0mm SMD
引用元:OptoSupply社のデータシート
ワテは表面実装部品のサイズ表記には今でも良く混乱する。
表面実装部品のサイズ表記はインチ表記とミリ表記が混在しているので混乱の元なのだ。
電子部品最大手のロームさんのサイトに分かり易い表があったので以下に引用させて頂く。
ローム品名 | チップサイズ | mm | inch | |
---|---|---|---|---|
L | W | |||
***004 | 0.4mm × 0.2mm | 0402 | 01005 | |
***006 | 0.6mm × 0.3mm | 0603 | 0201 | |
***01 | 1.0mm × 0.5mm | 1005 | 0402 | |
***03 | 1.6mm × 0.8mm | 1608 | 0603 | |
***10 | 2.0mm × 1.2mm | 2012 | 0805 | |
***18 | 3.2mm × 1.6mm | 3216 | 1206 | |
***25 | 3.2mm × 2.5mm | 3225 | 1210 | |
***50 | 5.0mm × 2.5mm | 5025 | 2010 | |
***100 | 6.4mm × 3.2mm | 6432 | 2512 |
表 チップ抵抗器 サイズ
引用元 https://www.rohm.co.jp/electronics-basics/resistors/r_what6
今回ワテが採用したチップLEDはインチ表記で0805、ミリ表記で2012だ。
どちらの表記も四桁の整数なのでややこしい。それに上表を見て分かるように0402や0603なんてのはミリ表記にもインチ表記にも全く同じ数字があるのだ。これは駄目だろ。
ミリで有る事を明示的に表す0603Mなどの表記もあるようだが、Mを省略して単に0603と書かれる場合もあるのだ。それを間違えて基板を設計してしまうと、基板に配置した電極サイズと実際の部品サイズが違ってしまう問題が生じる。
さて、KiCadの最新版8.0.4では下図に示すように0805サイズの表面実装型LEDのフットプリントは幾つかあるが、0805_2012Metricと書いてあるので分かりやすい。今回は手ハンダ付けするのでその中でもHandSolderと言うやつを選んでいる。
図 LED_0805_2012Metric_Pad1.15×1.40mm_HandSolderを選んで基板を設計した
HandSolderが付いているフットプリントはHandSolderが付いていないやつに比べると、電極サイズが若干長めで手ハンダ付けし易いのだ。
チップ部品のハンダ付けの手順は簡単で、まずは下写真のようにダイオードD2の一方の電極にハンダを盛る。
写真 D2ダイオードの一方の電極にハンダを盛る
その上にチップ部品を載せて、必要ならフラックスを塗布する。そして部品の片側をハンダ付けしたら、もう一方の電極もハンダ付けすれば完了だ(下写真)。
写真 0805(2012M)サイズのチップLEDのハンダ付け成功
上写真を見ると、少々ハンダの量が多いが、まあしっかりハンダ付け出来ているので良しとする。
ハンダ付けに使っている工具やハンダゴテ紹介
ワテが表面実装部品を使うようになったのは数年前の事だ。
その当時はリード型の抵抗やコンデンサなどしか使ったことが無かったので、米粒くらい小さい表面実装部品なんてハンダ付け出来るのかなあと思っていたが、やってみると案外簡単だった。
下写真は先程のLEDに加えて10μのセラミックチップコンデンサや22KΩチップ抵抗をハンダ付けした様子を示す。
写真 チップ部品を手ハンダ付けするのは案外簡単に出来る
下写真はワテがハンダ付けに使っているピンセットや爪楊枝だ。
写真 ワテがハンダ付けに使っているピンセットや爪楊枝など
上写真の大きなピンセットは確かダイソーで100円で買ったやつだが、持ち手が長いので何かと使いやすい。
あと、表面実装部品を扱うなら実体顕微鏡は必須だと思う。10代や20代の人なら裸眼でも米粒くらいの表面実装部品を扱えるかもしれないが、視力が低下した今ではワテには実体顕微鏡は無くてはならない。
写真 引き出しスライドレールを利用して自作した実体顕微鏡スタンド
上写真の引き出しスライドレール式実体顕微鏡スタンドは別の製作記事で紹介しているので興味ある人は御覧ください。
下写真がワテが使っているハンダゴテのコテ先だ。
写真 白光のBC型(T12-BC2)やD型(T12-D24Z)コテ先
上写真のように大小2種類のハンダゴテを使っている。
BC型は先端を斜めカットしたやつだ。D型は先端がマイナスドライバーのような形状だ。
ワテは表面実装部品の場合でもD型の大きい方のコテ先を使う場合が多い。
部品が密集していて大きなコテ先だと作業がやり辛いなどの場合には小さい方のBC型のコテ先を使う。
白光 D型 コテ先 をアマゾンで見る。
白光 BC型 コテ先 をアマゾンで見る。
表面実装部品を手ハンダ付けするコツ
表面実装部品を手ハンダ付けするテクニックを紹介しよう。
なおここで紹介するテクニックはワテ流なので、世間一般の標準的な手法かどうかは分からない。
まず、二箇所ある電極の一方に事前にハンダを盛っておいて、そこにチップコンデンサ(3216M)を載せた。
そして、下写真のようにD型コテ先を当ててハンダを溶かす。ちなみにこの写真はD型コテ先を後から重ねた合成写真だが。
写真 チップコンデンサの一方の電極をハンダ付けする
上写真のように右手に持ったハンダゴテのコテ先をチップ部品に当てると、当然ながらチップ部品は動いてしまう。
従来のワテはこの時点で左手に持ったピンセットなどでチップ部品が動かないように押さえていたのだが、それは難しい。
なぜなら右手でハンダゴテ、左手でピンセットを持って小さなチップ部品をまっすぐに固定するなんてのは、やってみると分かるがそう簡単ではないからだ。
なので、今では下写真のように左手に持った爪楊枝でチップ部品押さえておいてハンダゴテを当てる手法を採用している。
写真 左手に持った爪楊枝でチップ部品を押さえておくとやりやすい
金属のピンセットや精密ドライバーなどよりも爪楊枝なら木製なので部品に対するダメージも無いので安心だ。
下写真のように片側の電極がハンダ付け出来た。
写真 片側の電極がハンダ付け出来た
あとはもう一方の電極をハンダ付けすれば良いのだが、ここで注意すべきことは短時間でハンダ付けを終える必要がある。具体的には1秒以内くらいか。
もし2秒も3秒も熱するとチップ部品全体が熱せられて、先程ハンダ付けを終えた反対側電極のハンダも溶けてしまい部品が動いてしまうからだ。
写真 もう一方の電極を1秒以内くらいの短時間でハンダ付けする
そうすると下写真のようにチップコンデンサを所定の位置に取り付け成功した。
写真 チップコンデンサを所定の位置に取り付け成功した
上写真において、最初にハンダ付けした下側電極のハンダの形状がいびつなので、必要なら再ハンダ付けして形を整えても良い。
ハンダを盛り過ぎた場合にはハンダ吸い取り銅網線を使って除去すれば良い。
これらのハンダ付け作業で重要な事は、ハンダゴテを当てやすいように基板の向きを毎回微調整することだ。でも基板を動かすのが煩わしいから多少無理な姿勢でもハンダ付け出来るだろうと思ってやると失敗しやすい。
なので面倒臭がらずにハンダ付けがやりやすい位置に基板を動かしたり回転させたりする事が重要だ。
下写真はワテが使っている工具類。木製スタンドは自作した。
写真 ワテが使っている工具類と自作木製スタンド
精密ドライバーは赤黒の熱収縮チューブを使ってプラスは赤、マイナスは黒で色分けしている。
ICソケット、スイッチ類などの大型パーツをハンダ付けして完成
さて、ここまででチップ部品のはんだ付けが完了したのであとは大型部品のハンダ付けだ。
写真 マスキングテープを使ってトグルスイッチが抜け落ちないように固定
トグルスイッチ、DCジャック、DIP型ICソケット、タクトスイッチなどをハンダ付けしたら下写真のように完成した。
写真 ハンダ付けが完了したリモコン式ラッチリレー式4ch入力セレクター基板
この基板は実験的な意味合いもあるのでATmega328Pはゼロプレッシャーソケットで交換可能にしている。
この実験基板が無事に正常動作した場合には、バージョン2としてよりコンパクトな基板に設計し直す予定だ。
フラックスをパーツクリーナーで洗い落とす
ハンダ付けが終わったらフラックスを洗い流す。
ワテのお勧めはスプレー式のフラックスクリーナーだ。
写真 スプレー式フラックスクリーナーで基板のフラックスを洗い流す
フラックスクリーナー をアマゾンで見る。
IPA(イソプロピルアルコール) をアマゾンでで見る。
ちなみにフラックスクリーナーの主成分はイソプロピルアルコールなので18リットルの一斗缶入りを6千円程度で買うのが最も割安かも。
下写真のようにフラックスクリーナーをスプレーで基板に噴射する。
写真 フラックスクリーナーをスプレーで基板に噴射する
下写真のように歯ブラシでフラックスを擦る。
写真 歯ブラシでフラックスを擦る
フラックスが蒸発する前にティッシュや綿ウエスなどで汚れを拭き取る。
この作業を2~3回繰り返すと基板はかなり綺麗になる(下写真)。
写真 フラックスのクリーニングが完了した基板
ちなみにイソプロピルアルコールはアルコールではあるが飲用は不可だ。
赤外線リモコン式4入力オーディオセレクター(ラッチリレー採用)の動作実験
さて、いよいよ肝心の動作確認だ。
ICソケットには事前に秋月電子や共立エレショップなどで購入しておいたDIP型ICを装着した。
リモコンは二種類用意した。銀色の小型のやつは2メートルくらいしか飛ばない。
エレコムのやつは各社対応のテレビリモコンというやつだ。こちらは5メートルくらい離れても受信出来る。
4つの黄色のタクトスイッチ押下やリモコンボタン1~4の押下でリレーが選択される。
選択状態を赤色LEDで示す。さらにリレーにも動作確認用に緑LEDを付けているので選択された緑LEDが点灯する。
写真 ICなどの部品を装着したリモコン式4chセレクター基板(ラッチリレー採用)とリモコン
ATmega328Pを制御するプログラムは前回記事で紹介したようにライターPICKIT5と開発環境MPLAB X IDEを使って事前に少し開発していた。
まずは液晶キャラクターディスプレイに文字表示させるプログラムを書き込んだら書き込み成功し正常動作した。ただし、今回のセレクター機能ではこの液晶ディスプレイは使っていない。
次にプッシュボタン押下でリレーを切り替えるプログラムを書き込んでみたが全く動かん。
あちゃ~、お先真っ暗やと思ったのだが、MPLAB X IDEのデバッガなど使いながら地道に問題を解決して行ったところ、一週間ほどである程度動く状態まで持ってくることが出来た。ただし選択リレーを赤色LEDで表示する機能が正しく動かない。
プッシュボタン押下でリレー切り替えは出来るようになったがその位置の赤色LEDが正しく点灯せず、一瞬点灯して消えてしまう。その理由はプログラムのバグと回路図にも間違いが有ったのだ。回路図の間違い部分は外付け抵抗を追加してやれば解決し、無事にプッシュボタン押下でリレー切り替えや赤色LED表示が動くようになった。
なお、デバッグ中に別の配線間違いがあることが判明し、4つある黄色のタクトスイッチの1番目(左端)のSW1が効かないのだ。解決策は分かったのだがこの基板は未修正状態なのでSW1にはラッチリレーが反応しない問題が残っている。
次にリモコン信号受信でリレー切り替えをする部分だが、これも事前に作成していたプログラムを書き込んだのだが、全く動かないのだ。もうやる気も失せるくらい落ち込んだが、ここで諦めれば何の進歩もない。気力を出してデバッグを続けた。
試しにオシロスコープを使って赤外線受信LEDの出力端子をモニターすると、リモコンボタン押下に応じて出力信号を出している。なのでリモコン信号の受信には成功しているのだ。ところが何故かその信号をATmega328Pに読み取れない。
最終的に分かったのは、ワテ所有のATmega328Pは数個あるのだが、何故か特定の1個のATmega328Pを使うとリモコン信号を受信してもその信号を読み取る事が出来ないのだ。原因は調査中だが、当初はそのATmega328Pを使っていたので問題が複雑化してしまった。
兎に角、一週間ほど悪戦苦闘した結果、リモコン受信も成功してリレー切り替えも出来るようになったのだ。
電源をONすると下写真のように一番目の赤いLEDが点灯しているが、これはSW1の配線間違いの影響で点灯してしまっている。本来は点灯しないのが正解だ。
写真 電源ONすると一番目LEDが点灯する問題はあるが他の機能は正常動作する
では、下の動画で電源ONするところからリモコン操作でLEDが切り替わる様子を紹介しよう。
動画 リモコン式4chセレクターの動作の様子
電源ONすると一番目赤LEDが点灯する問題はあるが、その後、リモコン(ELECOM)ボタンを順番に2, 3, 4, 3, 2, 1と押すとそれに応じてラッチリレーが切り替わると同時に赤色LEDや緑色LEDも切り替わるのが分かるだろう。
動画には撮っていないが、黄色タクトスイッチも2, 3, 4番を押すと同じくラッチリレーが切り替わる。ただし1番スイッチは配線間違いの問題があるので反応しない。
と言う事で、ワテにとっては初めての大掛かりなデジタル回路を設計したのだが、当初の目的をほぼ達成することが出来たのだ。
素晴らしいぞ。
ワテもやれば出来るぞ。
まとめ
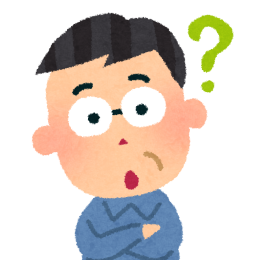
ワンチップマイコンATmega328Pを使ったデジタル回路がほぼ期待通りに動いたのは感動的だ!
当記事はラッチリレーを採用した赤外線リモコン式4入力オーディオセレクター製作プロジェクトの二回目記事だ。
PCBWayさんに発注してわずか6日で自宅に届いた専用基板に部品をハンダ付けした。
ホットプレートリフローで三端子レギュレータをはんだ付けし、他の表面実装部品も手ハンダ付けした。
ATmega328Pワンチップマイコンの制御プログラムは前回記事で紹介したように事前にブレッドボードを使った予備実験において開発していたので、そのプログラムを今回少し手直しして流用した。
そして動作確認したところ最初は全く動かなかったのでお先真っ暗だったのだが、地道にデバッグした結果、二箇所の回路設計ミスを発見した。プログラムにもバグが潜んでいた。
回路設計ミスの一箇所は外付け抵抗を追加して修正し、もう一箇所は基板上では修正はしていないが回路図の修正の目処は立っている。
その結果、動画で紹介したようにリモコンボタンに反応して1, 2, 3, 4とラッチリレーを切り替える事に成功した。かつ、現在選択中のリレー位置を示す赤色LEDも正常に点灯するようになった。
だたしタクトスイッチSW1周りに配線間違いがあるので現状ではSW1は効かない。リモコンボタン1は効くが。
と言う事で、ワテにとってはかなり本格的なデジタル回路を使ったプロジェクトであるが、いい感じで出来上がってきた。
今後の予定としては、SW1が効くようにこの基板の配線間違いを手作業で修正する作業を予定している。
追記 2024/8/5
その後、SW1問題を修正するために下写真のようにICソケットを用いて配線変更した。
![]() |
![]() |
新しいICソケットを用いて配線変更 | そのICソケットを既存のソケットに二段重ね |
写真 SW1周りの配線間違いをICソケット二段重ねで修正
その結果、SW1も正常に動作するように出来た。電源ON直後の赤色LEDも非点灯に出来た。素晴らしい。
なお、なぜプリント基板配線を直接にカット・追加する方式ではなくICソケット二段重ねで配線変更したのかと言うと、配線変更箇所が基板部品面にありその場所は既存のICソケット下に隠れていたのでICのソケットを取り外さないと修正が困難。そこで新しいICソケットを二段重ねにする方式で解決したのだ。我ながら素晴らしいアイデアだと思う。自画自賛。
追記ここまで
それと並行して、DIP型デジタルICを表面実装型のフラットパッケージに置き換えたコンパクトな基板(バージョン2)の設計を予定している。実は既にある程度は完了している。
それらが完了したらバージョン2基板をPCBWayさんに発注して、その基板を使ってリモコン式のスピーカーセレクターを作りたいと思っている。
シャーシも見栄えの良いやつを作るか買うかしたいと思っている。
良い作品が完成したら販売しようかな。
購入希望者さんが有るかどうか分からないが。
(続く)
コメント