
ワレコ
今日は曇り空で涼しい。
電子工作には最適の日だ。
さて、現在製作中の「LM317可変三端子レギュレータとオペアンプを使ったCV/CC直流安定化電源」であるが、ALLPCBさんに発注していたプリント基板が先日到着したので早速製作に取り掛かった。
KiCadを使ったプリント基板設計(前回記事)はこちら↴
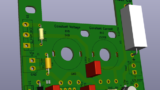
今回製作する電源装置の場合には、出力電圧は1.25~20VDCくらいを想定している。
CV/CC電源とはConstant Voltage(定電源)、Constant Current(定電流)電源と言う意味で、通常は定電圧電源として動作する。つまり電圧設定用のボリュームを回すと出力電圧が増加する。
CV/CC電源には電圧設定ボリュームだけでなく、電流制限用のボリュームも付いている。そのボリュームによって出力電流値を制限する事が出来る。もし出力電流が設定値を超えそうになると、自動的に定電圧モードから定電流モードに移行して出力電圧を減らす事で、電流値を設定値以下に保つ動作になる。
と言う訳で、早速製作に取り掛かった。
結論としては専用基板を使ったおかげで製作は順調に行き作業時間も短く、いい感じで動作したぞ。
では本題に入ろう。
CV/CC直流安定化電源の基板到着
ALLPCBさんからプリント基板が到着
下写真がFEDEXで到着したALLPCBさんの小包だ。
写真 FEDEXで到着したALLPCBさんの小包
今回は三種類のプリント基板を発注した(下写真)。
写真 今回発注した三種類のプリント基板(ALLPCB製)
上写真に示すように各十枚のプリント基板はエアーキャップで厳重に真空パックされている。その結果、輸送中の振動で互いに基板が擦れるなどの心配が無い。
プリント基板を使ってシャーシパネルを作成した
下写真左の緑基板がCV/CC電源制御回路の基板だ。
写真 左:CV・CC制御基板、中:フロントパネル、右:リアパネル(ALLPCB製)
一方、上写真の中央と右端の白色基板は、それぞれフロントパネルとリアパネルに使う。
つまり、中央基板の大きな長方形の角穴にはアマゾンで買ったデジタル電圧・電流計を嵌め込む。
それ以外の角穴や丸穴にはロッカースイッチ、トグルスイッチ、LED、ボリューム、ジョンソンターミナルなどを取り付けるのだ。
一方、右端の基板はリアパネルとして使うので、多数の通風孔を格子状に開けてみた。
下部にはDCジャック取り付け穴を設けたので、その部分から外部電源を用いてDC24V程度を入力する。
三枚の基板を仮組み立てしてみる
下写真のように直流用のデジタル電圧電流計をフロントパネル基板に嵌め込んでみた。
写真 直流用のデジタル電圧電流計をフロントパネル基板に嵌め込んだ
いい感じだ!
それにしても、このデジタル電圧電流計は安いなあ。三個で千円だぞ。一個約333円。
今回は使わないが、同じく交流用のデジタル電圧電流計も安かったので二個セットを買っておいた(下写真)。
なお、下写真に示すようにデジタルパネルメーターの上部と下部にはパネルに取り付けた後に抜け落ち防止の突起がある。
写真 デジタルパネルメーターの上部と下部の抜け落ち防止の突起をホットナイフで削る
事前にパネルメーターの縦横をノギスで実測してプリント基板に開ける長方形穴の寸法を決めたのだが、少々クリアランスが少な過ぎたようだ。
無理やりパネルメーターを押し込めば入ったかもしれないが、脱着出来ないとメンテナンス性が悪い。
そこで突起部分を少し削り取る事にした。
本当なら下写真のような専用のホットナイフを使うと良いのだが、手持ちに無かった。
そこで上写真のように60Wハンダゴテの先端にカッターの刃をネジ止めして、即席のホットナイフを自作した。そして、ABS樹脂の突起部分を熱で溶かしながら削り取った。
プリント基板をパネルに使う作戦は素晴らしい
その結果、下写真のように無事にパネルメーターを基板に装着出来た。
写真 DC用デジタルパネルメーターを嵌め込んだフロントパネル(裏側から)
下写真のように、電源用ロッカースイッチ、ジョンソン端子、トグルスイッチ、LED表示、パワートランジスタなどを挿し込んで、全体を仮に組み上げてみた。
写真 フロントパネル、制御基板、リアパネルの三枚を仮組した
おお、素晴らしい!
従来のワテなら、アルミシャーシに鉄工ドリルで丸穴を開けたり、角穴を開けたい場合にはハンドニブラで切り取るなどの作業でやっていた。
でも、そんな作業ではどんなに丁寧に作業しても、素人の手作り感が丸出しになるのは否めない。まあそう言う作業自体も電子工作の楽しみと言う人もいるとは思うが。
でも多分、多くの人はシャーシ加工はなるべくならやりたくないと思っていると思う。
それを解決するのが、プリント基板を使ってパネルを製作する手法だ!
今回作成したパネルの仕様は、以下の通り。
- 白色レジスト
- 黒色シルク文字
- 1.6mm厚
この基板も十枚で5ドル前後の製作費用なので格安だ。
現状では側面が開放状態なので、例えばこの部分には3Dプリンタでカバー形状のものを印刷して取り付けるなどしても良さそう。
あるいは、下写真のように前後パネルが平面状の構造の市販シャーシを買って、その前後パネル部分をプリント基板で作成して交換すると見た目の良い作品を作れるだろう。
なお、当初は下写真のように緑基板に載せる部品はリアパネル側に向ける予定であった。
写真 緑基板の部品をリアパネル側に向ける当初の案(中止)
つまり、緑基板の半田面がフロントパネル側に来る配置だ。
で、本当なら緑基板を出来るだけフロントパネル側に寄せて薄型の構造にする予定であったのだ。
その為に緑基板にも長方形穴を開けてあり、この部分にデジタルパネルメーターが通る予定だった。
そうすると、二個のボリューム軸もフロントパネルから出るので都合が良い。
ところが、上写真を見ると分かるように、フロントパネル裏側にはデジタルパネルメーター以外にも、ジョンソンターミナル、ロッカースイッチなどが出っ張っているので、緑基板はそんなにはフロントパネルには寄せられない。
要するに設計ミスをしてしまったのだ。
あかんがな!
まあ、人生そう言う失敗もある。
写真 フロントパネル裏側には各種部品が出っ張っている
と言う訳で、上写真で示した基板や部品の配置は不採用とした。
ではどのように対処したのかと言うと、それは以下で明らかになる。
なお、上写真の緑基板に「manufactured by ALLPCB」の文字があるが、これはワテがALLPCBさんに発注した事をメモする目的で入れている。ALLPCBさんに基板を発注すると自動的にこの文字が印刷される訳では無いです。
CV/CC直流安定化電源の製作
では、さっそく定電圧・定電流電源の製作を開始する。
抵抗・コンデンサは必ず値を計測してから取り付ける
ワテの場合は、電子工作をやる時には、抵抗やコンデンサは必ず値を計測してから半田付けするようにしている。
写真 ワテ自作のテスター計測ステーションを使って抵抗値を計測中
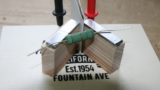
この金属皮膜抵抗(±1%)の抵抗値は以下の通り。
写真 使う抵抗は事前に値を必ず計測してから使う
今回製作する基板には33Ωと330KΩの抵抗を使う。似たようなカラーコードなので、いつも以上に注意を払いながら半田付けを行う。
抵抗の足を曲げるにはサンハヤトのリードベンダーが必須だ。
写真 サンハヤト リードベンダー RB-5は電子工作には必須のアイテム
電子工作をやる人でサンハヤトのリードベンダーRB-5を知らない人は素人と言っても良いだろう。
抵抗を半田付けする
プリント基板に抵抗を挿し込んでマスキングテープで固定する(下写真)。
写真 プリント基板に抵抗を挿し込んでマスキングテープで固定
このようにマスキングテープで部品を固定しておくと基板を裏返しても部品が抜け落ちない。
あとは、半田ゴテを使って半田付けを行えば良い。
写真 半田付けする前の抵抗のリード線
今回ALLPCBさんで製作したプリント基板は1.6mm厚の両面スルーホール基板で、半田の乗りもよく半田付けがやり易かった。
写真 リード型抵抗を半田付けした(ALLPCB製プリント基板、両面スルーホール1.6mm厚)
上写真において、白色シクル文字のサイズは以下の通り。
幅 1.0 mm
太さ 0.15 mm
上写真のように高さ1mmの小さなシルク文字も非常に綺麗に印刷されている。
なお、LED取り付け部分には ━▶┃━ のようにLEDの記号を描いておいた。というのはLEDやダイオードの取り付け向きをよく間違えそうになるので。
ちなみにこのLED(オレンジ色)は定電流モード(CC = Constant Current)になった時に光る。
あとは、8Pin DIPのICソケット(オペアンプLT1006用)や可変三端子レギュレーターLM350(LM317でも良い)、コンデンサ類を取り付けた。
ボリュームを取り付ける
次は二個のボリュームを取り付ける。
写真 電圧設定、電流設定の二個のボリュームを取り付け中
事前にボリュームの寸法をノギスで計測して設計したプリント基板に、上写真のようにピッタリとボリュームを取り付ける事が出来ると、極上の快感がある。
デジタルノギスは一本千円くらいで買えるので、ニ~三本常備しておくと便利だ。
写真 対角10mmのナットドライバーを使ってボリュームを固定
ボリュームには回転防止の突起が付いているが、上写真のようにプリント基板には二個の小穴を開けている。
その結果、ボリュームを基板に対してどちら向きにでも取り付けられる。
実際、この後でボリュームの向きは上写真とは逆向きに取り付ける事にした。
出力端子・スイッチ類を取り付ける
緑基板に部品の半田付けが完了したので、次はフロントパネルに各部品を取り付ける。
この場合にも事前に取り付け予定の部品の寸法を調べておいて基板に取り付け穴を開けたので、下写真のようにピッタリと嵌っている。完璧や!
写真 ジョンソンターミナルの対辺11mmの六角ナットをメガネレンチで締める
上写真のように設計通りに差し込む事が出来たジョンソンターミナルの六角ナットをメガネレンチででキッチリと締めて固定できると、ここでも快感がある。
もしアルミパネルに鉄工ドリルで穴開けした場合だと、穴が小さすぎてやり直すとか、大き過ぎて取り付けた部品の安定性が悪いなどの失敗もあるが、1.6mm厚の分厚い基板なので安定性も良い。
下写真のようにLEDの接続部分は2pinのピンヘッダーを使ってソケット式にした。
写真 メンテナンス性を考慮してLED接続部分は2pinのピンヘッダーのソケット式にした
ワテが使っているのが下写真の精密圧着ペンチだ。
この手の工具は値段が数千円と高いけれど、一生物なのである程度は良い製品を買っておく方が良い。
各部品を配線でつなぐ
緑基板と白色パネルを配線で接続する。
写真 緑基板と白色パネルを配線で接続
下写真のようにこの時点でも、緑基板の部品は後ろ側(リアパネル側)を向いている。
でも、この配置では組み立て辛かったのでこの後で緑基板を裏返す。つまり部品面がフロント側に来る配置にするのだ。
写真 緑基板とフロントパネルを接続中(この後、緑基板を裏返す)
下写真のように緑基板にはボリュームを直接取り付ける構造にしたので、その部分の配線作業を簡略化出来た。
写真 緑基板にはボリュームも載せたので配線が楽ちん
なお、ボリュームの取り付け向きもこの後で逆転した。
パワートランジスタにヒートシンクを付ける
さて、パワートランジスタを取り付けたのだが、下写真のように緑基板とフロントパネルとの距離が今までの写真よりも広がっているのが分るだろう。
写真 緑基板と白色パネルの間隔を75mmにした
今まで登場した写真では緑基板とフロントパネルは30mmの六角樹脂スペーサーで固定していた。
それを上写真のように75mmの金属製六角スペーサーに交換すると同時に、緑基板を裏返して部品面がフロントパネル側に来るようにした。その結果、ボリューム取り付け向きも変更した。
こう言う事態を想定して、ボリュームをどっち向きにでも取り付けられるように設計していたのだ。
見掛けに拠らず慎重派のワテである。
さて、下写真のようにパワートランジスタ(2SA1943-[BCE]-230V150W15A)は放熱板を付けやすいように基板の端に配置している。
写真 パワートランジスタにヒートシンクを付ける準備
下写真のヒートシンクはちょっと小さすぎると思うが、手持ちには手頃なサイズのやつが無かったので取り敢えずこのヒートシンクを付ける。
写真 手頃なサイズのヒートシングが手持ちに無かったので取り敢えず実験用に付ける
でもやはりこれだと小さすぎるので、さらにもう一つのヒートシンクを下写真のように付ける事にした。
写真 小型ヒートシンクを二個使って放熱効果を高める
そして下写真のようにヒートシンクを取り付けた。
写真 ヒートシンクを取り付けたパワートランジスタ
このCVCC電源は設計では最大20V5A程度まで出力出来るので、上写真のヒートシンクだとちょっと小さい。もし本番で大電流を流す時には放熱板の大型化を図りたい。あるいは小型ファンを付けるなど検討したい。
アルミパイプでボリューム延長シャフトを自作
ヒートシンクの取り付けは完了したが、75mmのスペーサーを使ったので二個のボリューム軸がフロントパネルから50mmくらい離れてしまった。
そこでΦ7のアルミパイプが手持ちにあったので、それを使ってボリューム軸を延長する。
写真 パイプカッターでΦ7アルミパイプを切断する
下写真のようなパイプカッターを一つ持っているとDIYには何かと役立つ。
ボリューム軸はΦ6mm、Φ7アルミパイプは内径Φ6なので、ボリューム軸にはピッタリ刺さる。
でも引っ掛かりが無いので空回りするので、その対策として下写真のようにアルミパイプの端に穴を開けて針金を通した。
写真 ボリューム軸延長用のアルミパイプΦ7と回転防止用に使う銅針金
下写真のようにΦ1.5のドリルを使ってアルミパイプに穴を開けて、そこにΦ0.9の銅針金を通した。
写真 Φ1.5のドリルを使ってアルミパイプに穴を開けてΦ0.9の銅針金を通した
その銅針金付のアルミパイプを下写真のようにボリューム軸の切り込み部分に嵌め込んだ。
写真 銅針金をボリューム軸の切り込みに嵌め込む
銅針金がボリューム軸の切り込みにピッタリと嵌るので回転させた時に空回りしなくなった。
完璧や!
一方、下写真のようにフロントパネル部にはΦ6軸用のツマミを付けたいので、Φ6銅パイプを短く切ってΦ7アルミパイプに差し込んだ。
写真 フロント部ではΦ6銅パイプを使ってΦ6用ツマミに合わせる
パイプ同士を差し込むだけだと空回りするので接着剤で貼る事を考えたのだが、それだと分解し辛い。
そこでΦ7アルミパイプに薄いポリエチレン袋の破片を挿し込んで、そこにΦ6銅パイプを挿し込んで摩擦で保持するようにした。
取り敢えず配線完了したCVCC電源
下写真のように三枚の基板と六角スペーサーを使って、無事にCVCC電源が組み上がった。
写真 三枚の基板と六角スペーサーを使って組み上げたCVCC電源
プリント基板をシャーシパネルに使う手法は予想以上にやり易かった。
もしシャーシ加工を従来のようにアルミシャーシに自分で穴開け加工するやり方でやっていたとしたら、シャーシ加工だけでも数日を要したと思う。
それが事前にKiCadを使ってパソコン画面上で各部品のサイズなどを考慮して取り付け位置など検討して注意深く設計図を描いたので、実物のパネル基板を使って組み立てる作業では大きなトラブルも無く、僅か数時間の作業で完成したのだ。
写真 リアパネルに開けた多数の通気口部分
上写真のリアパネルも1.6mm厚のスルーホール基板だ。
通気口はドリル穴Φ5/ランド径Φ7と言う大きなサイズのビアを定義して、そのビアを格子状に多数並べて開けている。
上写真の通気口のスルーホール部分を注意深く観察すると、ビアで作成しているのでスルーホール部分にも有鉛ハンダメッキが綺麗に施されているのが分るだろう。
その部分だけを見ると、金属製のパネルのような見栄えだ。物凄く高級感あるリアパネルになった。
もしランドの仕上をハンダメッキでは無くて金メッキにすれば、キンキラキンの超高級パネルになるぞ!
いつかやってみたい。
と言う事で、組み立て作業は無事に完了した。
写真 組み立て終わったCVCC電源
下写真のようにフロントパネルには市販のCVCC電源にあるようなスイッチ類やLED表示を付けている。
写真 完成したCVCC電源のフロントパネル部
フロント部の主な仕様は以下の通り。
- 黒色ロッカースイッチは主電源
- 赤ボリュームは電圧設定(デジタルパネルの電圧表示の赤色LEDに合わせた)
- 青ボリュームは電流設定(デジタルパネルの電流表示の青色LEDに合わせた)
- オレンジLEDはCCモードで発光
- トグルスイッチは出力電圧のON/OFF
- その上の白色LED(発光時は赤)は出力ONの表示
- 電圧出力端子は、ジョンソンターミナル(バナナプラグ用)とチップジャックの二種類を用意
CV/CC直流安定化電源の動作確認
組み立て完了したので、作業机の上を清掃して工具類は片付けた。
そして少し休憩して精神統一を図る。
入力DC20V、負荷10Ωで実験開始
下写真のようにCVCC電源の背面からDC20Vを入れておく。本当なら24Vくらいまで行けるのだが、あまり高い電圧だとパワートランジスタの発熱も大きいので少し電圧を下げたのだ。それに20Vのほうが切が良いので分かり易いし。つまり20Vで1A流れたら20Wと言うように計算し易いから。
写真 CVCC電源の背面からDC20V、負荷は10Ωを接続
上写真に少し写っているのがぺるけ式アンプ試験ワークベンチだ。
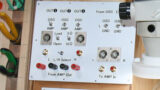
ぺるけ式アンプ試験ワークベンチを使う
下写真に示すぺるけ式アンプ試験ワークベンチには5Ωと10Ωの負荷抵抗を内蔵している。
写真 ワテ自作のぺるけ式アンプ試験ワークベンチの10Ω負荷を使う
この10Ω抵抗は電力200Wの巨大メタルクラッド抵抗なので、数アンペアくらいの電流を流しても殆ど発熱しない。
ワテ所有の高砂製作所の定電圧電源からDC20Vを出力する。
写真 高砂製作所の定電圧電源からDC20Vを出力
いよいよ実験開始だ(下写真)。
写真 実験用の配線接続が出来たので電源SWをONする前
いよいよ主電源SW(黒色ロッカースイッチ)を入れる。
緊張の一瞬だ。
電圧調整ボリューム最小位置
主電源をONした。
その瞬間に高砂製作所電源の電圧/電流表示を見たが 20V / 0.1A くらいだったので一安心。
一方、ワテ自作のCVCC電源装置のデジタル表示は以下の通り。
写真 主電源ON直後のデジタル表示
上写真では赤色ボリューム(電圧設定用)は最小位置なので、出力電圧もLM350の最低出力電圧付近の値(1.25V)を示している。
OUTPUTスイッチONして負荷に電流を流す
いよいよOUTPUTトグルスイッチを上に倒して負荷に電圧を掛けた(下写真)。
写真 OUTPUTをONにして負荷に電圧印加(赤色LED点灯)
OUTPUTスイッチをONにして電圧を出力すると、赤色LEDが点灯するようにしている。
おお、ここまでは順調だ。
出力電圧5Vで0.5A流れた
下写真のように赤色ボリューム(電圧設定)を右に回して5Vを出力した。その時の電流が0.50Aなので、負荷10Ωを考慮すれば妥当な値だ。
写真 10Ω負荷に5V印加して0.5Aなので妥当な値だ
完璧や!
出力電圧10Vで1.0A流れた
さらに赤色ボリューム(電圧設定)を右に回して10Vで1.00Aになった。おお素晴らしい。
写真 10Ω負荷に10Vで1.00Aなので妥当な値だ
この時、パワートランジスタのヒートシンクを手で触ってみたが、アッチッチと言うほどでは無く、温かいかなあと言う程度だった。
出力電圧15Vで1.49A流れた
ここまでは設計通りに順調なので調子に乗ってさらに出力電圧を上げて15Vにした。
写真 10Ω負荷に15Vで1.49Aなので妥当な値だ
その結果、上写真のように1.49Aなのでここでも妥当な値だ。
昔のワテなら、ユニバーサル基板に手配線していたので配線間違いも多く、電源ONした瞬間に抵抗やトランジスタ燃えるとか、電解コンデンサが爆発したなどの失敗も多かった。
それがKiCadで設計した専用基板を使うようになってからは、基板設計時に入念にデザインルールチェックを行う事で配線間違いを完全に除去出来る。
つまり自分が描いた回路図が間違っていない限り、自分が設定したフットプリントの足の並びを間違えていない限りは、出来上がったプリント基板の配線パターンは正しいのだ。
そう言う専用基板を使うようになって以来、ワテの電子工作の成功率は100%近いのだ!
従来のユニバーサル基板の方式だと成功率は50%以下だった。つまり二回に一回は失敗。
失敗したプロジェクトはデバッグで原因究明出来て完成したものもあるが、多くの場合は、原因不明で製作断念と言うのが多い。
電流制限ボリュームを回して定電流モード(CC)を試す
さて、CVCC電源の定電流モード(CC, Constant Current)を試してみる。
現時点では、15V出力で1.49Aの電流が流れている。
ここで下写真のように電流設定用ボリューム(青色)を左に回して電流値を制限してみた。
写真 定電流モード(CCモード)では期待通りにLED点灯し電圧も自動で下がった
その瞬間、上写真のように電流が1.22Aになり出力電圧も15が12.3Vに自動で低下したぞ!
かつ、CCモード表示用のオレンジLEDが光ったし!
完璧や!
でもまあ、あまりにも調子に乗ると失敗の元なので、ここで休憩して一息入れる。
冷やしたCCレモンを飲むのだ!
さらに定電流ボリュームを絞って電流を1.0Aに減らす
CCレモンで一息入れたので実験再開。
さらに電流制限ボリューム(青色)を左に絞って、電流を1.00Aまで減らすと出力電圧は10.1Vまで低下した。これも10Ω負荷を考慮すると妥当な値だ。
写真 定電流モードも期待通りに動作している感じ
いや~、こんなに上手くCVCC制御機能が働くとは思っていなかった。
このCVCC電源を作るにあたり参考にしたNational Semiconductor社の技術文書にある回路では、LM301Aと言う両電源のオペアンプが使われていたが、それをLT1006と言う単電源オペアンプに交換したので、その辺りが最も心配であった。
でも今回の実験結果を見る限りは、正常に動作している感じだ。
まとめ

ワレコ
安定化電源は自作するよりもメーカー製の市販品を買う方が良いとは思うが、何事も挑戦なので今回敢えて自作した。
その結果、予想以上に順調に完成して、期待通りの動作をしたのだ!
当記事ではLM350可変三端子レギュレータのアプリケーションノートに掲載されている「5A Constant Voltage/Constant Current Regulator」の製作記事の後半だ。
前回記事では、自作に必要なプリント基板をKiCadで設計してALLPCBさんに発注するまでの過程を紹介した。
そのプリント基板が一週間くらいの速さで到着したので、お盆の休みを利用して一気に製作した。専用基板を使う事で電子工作は部品を半田付けするだけでほぼ完成するようになった。
従来のユニバーサル基板を使う手法では、部品の半田付けが終わっても、正常動作するかどうかは五分五分と言う感じ。電源投入は一か八かと言う危なっかしい作業だった。それが専用基板を用いるようになってからは、100%近い成功率になったのだ。
完成したCVCC電源の印象
フロントパネル、リアパネルもプリント基板で製作して、三枚の基板を六角スペーサーで連結すると言う構造は、手軽だし配線もやり易いのでお勧めだと思う。
今後の電子工作でもこの手法を使いたい。
一個約333円と言うデジタル電圧計電流計は色んな電子工作に活用できる。
完成したCVCC電源の改良点
当初の設計通りに完成して無事に正常動作した(と思う)ので、大きな反省点は無いが、今後の電子工作の為の改善点を上げてみる。
配線が複雑
三枚の基板間の配線が十本近くあるので複雑になった。理想的には配線無しで全部の部品を直接基板に半田付け出来るような構造なら組み立てが楽になる。
あるいは配線を使うとしても、全部の配線をソケット化すれば分解や組み立て作業が楽だが、今回は一部はソケット化したが、多くの配線は直接半田付けしている。なのでもし分解整備する場合には半田付けを外す必要もある。
粗調整、微調整用のボリュームがあると良い
電圧設定ボリューム、電流設定ボリュームは各一個だけだが、市販のCVCC電源なら電圧設定や電流設定にそれぞれCOARSE/FINEと言った粗調整、微調整用のボリュームが付いている物が多い。
今回も設計時点ではCOARSE/FINEのボリュームを付ける案も検討したのだが、そこまで拘って作っても、そもそも正常動作するかどうか半信半疑だったので、取り敢えず簡略化したバージョンで作成した。なので、もし類似のCVCC電源の製作を検討中の人は、COARSE/FINE調整も考慮すると良いと思う。
ヒートシンクが小さい
本格的なCVCC電源として活用するにはヒートシンクが少々小さい。なので、基板設計時点でパワートランジスタに取り付けるヒートシンクも選定しておいて、その形状や取り付け場所を考慮した上でシャーシを設計すべきだった。
感想
プリント基板をシャーシとして利用する手法は既に多くの人が採用している手法であるが、ワテも今回初めて試してみた。
その結果、想像以上にその手法は良い事が判明したので、今後も採用したい手法だ。
やっぱり電子工作が無事に完成して期待通りに動くと充実感がある。
その為には、KiCadなどのEDAソフトを活用して専用基板を設計するのが良い。
かつ、半田付け関連ツールにもある程度の投資をすべきだろう。
具体的にはステーションタイプの半田ごては必須だと思う。
(完)
コメント