
ワレコ
春が来た。
電子工作には最適の季節だ。
何故なら、半田付けの煙を換気する為に部屋の窓を全開に出来るからだ。
さて現在作成中の「ぺるけ式FET差動バランス型ヘッドホンアンプ」であるが、製作を始めたのが2020年9月頃なので約一年半前になる。
KiCadで基板を設計してPCBWayさんに発注した過程はこの記事で紹介している↴
なぜこんなに時間が掛かっているかと言うと、幾つか理由がある。
一つ目の理由は、アンプ基板、電源基板、ラッチリレー式入力セレクター回路基板、定電圧電源回路基板、など複数の基板を順番に設計して組み立てているので時間が掛かっている。
二番目の理由は、最近では、このぺるけ式FET差動バランス型ヘッドホンアンプの製作以外に、Arduino UNOやAVRマイコンを使った電子工作も挑戦したので、その間はこのアンプ製作プロジェクトは中断していたのだ。それ以外にも幾つかの電子工作をやっていた。
三番目の理由は、冬場は寒いので行動が鈍っていたのだ。冬眠中の熊さんか。
この「ぺるけ式FET差動バランス型ヘッドホンアンプ」の完成を目指して、さらに二種類のプリント基板とシャーシに使う前後のアルミパネル加工をPCBWayさんに発注していたのだが、それらが先日到着したので、アンプ製作に必要な部品は全て揃った。
当記事では、アンプの完成を目指して、まずはシャーシを組み立てたのでその製作過程を紹介したい。
ワテと同じようにオーディオ機器を自作している人で、完成度の高いシャーシを外注したい人向けに、アルミ板に穴開け加工や文字入れなどのデータ準備する上でのテクニックなど紹介したい。
そのデータを元にPCBWayさんにアルミ板加工を発注すればいい感じのシャーシを低価格で入手出来るのだ。
ヤフオクに出品中の専用プリント基板はこちら⤵
では、本題に入ろう。
PCBWayさんから届いたプリント基板とアルミパネル加工品の紹介
PCBWayさんに発注したのが約一ケ月前だ。
プリント基板のみの発注なら、一週間後くらいにはPCBWayさんから自宅に基板が届く。
写真 PCBWayさんから届いたFEDEXの小包
一方、アルミ板のレーザー加工とシルク印刷による文字入れ加工の場合には、発注時に表示された情報では予想納期は13から15日との事だった。
PCBWayさんには過去にもアルミ板に類似の加工を依頼した事が二度ある。
その時は約二週間から三週間程度で届いたので、今回は今までよりも若干日数がかかったようだ。
さて、段ボール箱を開封した(下写真)。
写真 PCBWayから届いたFEDEX小包を開封
上写真のように十分な量のクッション材で厳重に梱包されている。
下写真のように内容物を取り出した。それらも厳重にエアークッション材で包まれている。
写真 PCBWayから届いたプリント基板(二種類)とアルミ板加工品(二種類)
PCBWay製両面スルーホール基板(二種類)の紹介
まずはプリント基板を紹介しよう。
一つ目の基板は下写真に示すやつで、モーメンタリ型プッシュボタンスイッチを四個取り付けて、ぺるけ式FET差動バランス型ヘッドホンアンプの入力セレクター基板(ラッチリレー式)を切り替える用途に使う。
写真 四連プッシュボタン基板(PCBWay製両面スルーホール基板)とNKKスイッチ(BB-15AV)
PCBWayさんに基板を発注する場合、基板の色(=レジスト色)は緑、青、赤、紫、白、黒、黄、無しなどが選べる。
今回は「黄色」を選択した。PCBWayさんの黄色レジスト基板は、上下の写真に示すように、黄色と言うよりも昔ながらの薄茶色のベーク基板やフェノール基板っぽい色合いなので、ワテ好みなのだ。
注意事項としては、上写真の基板には「PCBWay」のロゴが印刷されているが、これはワテがPCBWayさんに発注した事をメモする目的で入れているだけだ。PCBWayさんに基板を発注すると自動的にこの文字が入る訳では無いので注意しておく。
次に下写真は表面実装型の三端子レギュレーターを二個搭載できる基板だ。これはラッチリレーの駆動に必要なDC5Vと、その制御回路(表面実装型の74HC00, 74HC14など使用)に必要なDC3.3Vを生成する目的で作った。
写真 5Vと3.3Vの三端子レギュレーター電源基板(PCBWay製両面スルーホール基板兼SMD基板)
上写真の基板の特徴としては、取り付ける部品は三端子レギュレーターも抵抗もコンデンサも表面実装型の部品を想定しているが、実は、リードタイプの部品も取り付けられるようにスルーホール穴も開けているのだ。
つまり表面実装部品、リード部品の両方が使える二刀流基板と言う事になる。
大谷翔平基板と呼んでくれ。
なんのこっちゃ。
なお、3.3V生成部の入力は必要なら5V出力から取れるように基板裏面に斜めでパターンを配置している。今回はその方式で3.3Vを生成する予定だ。
プリント基板の外注は簡単
まだプリント基板を外注した事が無い人は、是非やってみると良いだろう。
ワテの場合も二年ほど前までは電子工作をするならユニバーサル基板にスズメッキ線などで手配線していた。
トランジスタや抵抗、コンデンサなどの大き目のパーツならまあそのやり方でもどうにかなるが、ICを沢山使った基板を作成するとなると、手配線だと間違い易いし時間も掛かる。
それにピンピッチが2.54mmのICならDIP型のICソケットを使うなどでユニバーサル基板に取り付け可能だが、SSOPとかTSOPなどのピンピッチ1.27mmや0.65mmの小さな表面実装ICだと、ユニバーサル基板には載せられない。
そんな問題を全て解決してくれるのが、専用基板なのだ。
プリント基板設計ソフトは幾つかあるが、ワテのお勧めはKiCadだ。EagleやDesignSpark PCBも人気がある。
それらのEDAソフトを使って基板を設計して、基板データをガーバーデータ形式で出力する。
そのガーバーデータをPCBWayさんなどの基板製造業者さんのサイトにアップロードすれば約一週間後には自宅に5枚や10枚の両面スルーホール基板が届くのだ。
費用総額も約ニ千円程度(基板製作費用が5ドル前後、FEDEXやDHL送料が15ドル前後)。
当ブログの読者の飯野様も独学でKiCadをマスターされて無事にガーバーファイルの出力に成功し、PCBWayさんに発注出来たとの事だ。
是非皆さんもプリント基板を自分で設計してみると良い。
電子工作の新しい世界が広がる事は間違い無い。
PCBWay製のアルミ板加工品の紹介(二種類)
さて、電子工作にはプリント基板も使うが、そのプリント基板を収納するシャーシも必要になる。
最近のワテはPCBWayさんにアルミ板の
- レーザー切断加工(穴開けなど)
- アルマイト処理(色付け)
- 文字入れ(シルク印刷、レーザー刻印加工)
も発注する事が多い。
下写真が今回発注したフロントパネルとリアパネルの二枚のアルミ板(210x60x3ミリ厚)だ。
写真 ぺるけ式FET差動バランス型ヘッドホンアンプ用アルミパネル(PCBWay製)
製作費用は一枚当たり約70ドルだった。ちなみに過去にも同じサイズで類似のアルミ板加工を何度か発注したが、その時には一枚当たり50ドルから60ドルくらいだった。
今回費用が若干上がった理由は未確認だ。アルマイト加工で初めて指定したシャンパン色(Champagne)が高かったのかも知れない。あるいはレーザー切断加工では、切断距離に応じて費用が掛かる。つまり多数の穴が開いていると値段が高くなるのだ。
Size : | Quantity : | 1 | |
Material : | Aluminum 5052 | Color : | Silver white |
Process : | Surface finish : | Anodized – Bead blast + Anodized color – Champagne | |
Threads and Tapped Holes: | No | Tolerance: | No tighter tolerances required (ISO 2768-1) |
Inserts: | No | Inspection: | Standard Inspection (No paper report) |
Welding: | No | Thickness: | Subject to 3D file |
Finished appearance: | Standard | ||
Part Marking : | Silkscreen – Process Black | Additional comments : |
表 PCBWayさんにアルミ板加工発注のパラメータ(レーザー切断、アルマイト処理、シルク印刷)
このアルマイト加工のシャンパン色(Champagne)は、写真の通りかなり濃い目のオレンジ色だ。
本当は下写真に示すオーディオ機器のような薄いシャンペンゴールド色を期待していたのだが、実際は物凄く濃かった。残念!
まあ、アルマイト加工の仕上がりの色合いなどは、実際に注文してみないと分からないと思っていたので想定の範囲内だが。ホリエモンかよ!
それと予想以上に濃いオレンジ色に仕上がったが、まあ見慣れると中々いい感じの色合いに見えるし。良しとしよう。
PCBWayさんで金属加工を依頼する方法
PCBWayさんに金属加工を発注するには下図に示すNC・3Dプリントのメニューを開くと良い。
図 PCBWayさんのNC加工、3Dプリントなどのトップメニュー
今回は Sheet Metal Fabricationメニューから発注した。
その中でCADデータをアップロードする事が出来るので事前にCADで設計しておいたデータをアップロードすれば良い。ワテはFusion360を使っている。
今回製作依頼したような平板に穴開け加工だけの簡単な加工なら、三次元データとして設計しても良いし、あるいはもっと簡単に二次元データとして設計して厚みは別途数字で指定しても良い。
文字入れに関しては、シルクスクリーン印刷とレーザー刻印加工が選択可能だ。
シルクスクリーン印刷なら色んな色で文字入れが可能だ。
レーザー刻印加工は、アルマイト加工で付けた色をレーザーで焼き取ってアルミの地肌(銀色、実際は白っぽく見える)にする事で文字入れするので、黒アルマイト加工などの濃い目の表面処理を指定した場合には適していると思う。
今回のシャンペン色も実際は濃い目のオレンジ色なので、レーザーで銀色文字を入れてもいい感じに仕上がったと思う。
文字入れはレーザー刻印加工がお勧めかも知れない
下図はシルク印刷文字を拡大したものだ。
写真 拡大写真(上:リアパネル、下:フロントパネル)
上写真のように、フロントパネルの「A」の文字に若干の滲みがある。まあ良く見れば気になるが、これくらいは妥協しよう。
ちなみに下写真は以前にPCBWayさんに発注した「ぺるけ式トランジスタミニワッターPart5(19V版)」用シャーシのリアパネルとフロントパネルだ。
写真 上:銀色アルマイト加工に黒シルクスクリーン印刷、下:黒アルマイト加工にレーザー刻印加工(詳細はこの記事を参照)
上写真で銀色アルマイト加工のリアパネルには黒色シルクスクリーン印刷、黒アルマイト加工のフロントパネルにはレーザー刻印加工で文字が入っている。
写真のように銀色アルマイトパネルに印刷した黒色シルクスクリーン文字は「SPEAKER」の「E」の文字が大きく滲んでいる。
この時には、事前にPCBWayさんから連絡が来て、もし必要なら無料で作り直すとの提案が有ったのだが、まあ再作成して貰うと時間も掛かるし、背面なので目立たないから上写真のやつでOKした。
一方、黒色アルマイトパネルにレーザー刻印で入れた文字は滲む事も無く輪郭がシャープにくっきりと刻印出来ているのが分るだろう。
と言う事で、もし読者の皆さんがPCBWayさんに類似の金属加工を依頼する場合には、濃い目のアルマイト加工色(黒、オレンジ、青、紫、茶色、その他)にレーザー刻印加工で銀色文字入れすると綺麗に仕上がると思う。
シルクスクリーン印刷の場合には、ここで示した例のように文字の滲みが入る可能性がある。本当は滲む事無く綺麗に仕上がるのが望ましいが、少しくらいなら許容しておこう。なぜなら金属パネルに自分で文字入れ加工するなんてのは専用の機器を使わないと不可能だし、一枚当たり数千円の費用で穴開け、アルマイト色付け、文字印刷までやって貰えるのだから。
ちなみに下写真はパネルの裏側。
写真 ぺるけ式FET差動バランス型ヘッドホンアンプ用アルミパネル(PCBWay製)
シャンパン色(Champagne)を指定したが、上写真のようにかなり濃い目のオレンジ色に仕上がっている。
PCBWayさんにお願いしたいのだが、シャンパン色(Champagne)のアルマイト加工は、できれば下写真のような薄い色合いに仕上げて欲しい。
恐らくワテ以外の読者の皆さんも、もしオーディオ機器を自作するなら薄いシャンペンゴールドなアルミパネルを希望する人のほうが多いと思う。
サイドウッドを自作してシャーシを組み立てる
サイドウッドに塗装を行う
PCBWayさんで作って貰った二枚のアルミパネルを使ってシャーシを自作する。
サイドウッドはホームセンターで買ったエゾ松材を切り出して塗装して自作する。
写真 カンペハピオ 水性着色ニス 新オークを一回塗った
上写真は、カンペハピオ 水性着色ニス 新オーク を一回塗った直後の写真だ。
今までもこの塗料を使ったのだが、ワテの塗装技術が下手なのかも知れないがエゾ松材には均一に塗り辛い。
上写真では綺麗に塗れているように見えるが、実際はムラが多い。二回、三回と塗り重ねてもムラが出る。
刷毛でムラなく塗るのは難しいなあ。
そこで、下写真のように油性スプレーニスで上塗りしてみた。
写真 カンペハピオの油性ウレタン着色ニススプレー「新ウォルナット」を上塗りした
カンペハピオの油性ウレタン着色ニススプレー「新ウォルナット」を塗ってみる。
その結果、上写真のように均一には塗れたが表面が滑らかでは無く、若干ザラザラした感じになってしまった。何でかな?
塗装は奥が深い。
と言う訳で、まあ兎に角、茶色に塗れれば良いのでこの辺りで妥協して次のステップに進もう。
内側にMDFボードの小板を接着する
寸法は以下の通り。
MDFボード 297 x 54 x 5.5 mm
下写真のようにダイソーで買った5.5mm厚のMDFボードを丸ノコでカットして塗装済みサイドウッドの裏側に木工用ボンドで貼り付ける。
写真 MDFボードに木工用ボンドを歯ブラシで塗り広げる
下写真がMDFボード貼り付け済のサイドウッドや、シャーシ組み立てに必要なその他の全パーツだ。
写真 自作シャーシに使う全パーツ
上写真で白い板はアルミ複合板(297 x 210 x 3mm)だ。
類似品は例えばアマゾンでも売っている。
ワテはたまたまA4サイズ(297 x 210)を採用したが、300 x 200 などのサイズも沢山販売されている。
あるいはホームセンターでサブロク板(1820 x 910)サイズの巨大なアルミ複合板を買って来て自分で丸ノコでカットしても良い。あるいはホームセンターのカットサービスを利用しても良い。
シャーシを接着剤で組み立てる
下写真がワテがDIYで良く使う接着剤だ。
写真 今回は下側の超多用途セメダインスーパーXを使った
写真上のコニシ ボンドGPクリヤーは難接着材料のポリプロピレンも接着出来る優れものだ。
今回は写真下のセメダイン 超多用途接着剤 スーパーX クリアを使った。
この接着剤はその名の通り、色んな素材の接着に使える万能タイプなので一つ持っておくとDIYで活躍する。
下写真のようにセメダイン超多用途スーパーXを使って前後アルミパネル、左右サイドウッド、底板(アルミ複合板)を接着した。天板(アルミ複合板)は接着しないが形を整える為に嵌めている。
写真 接着剤が固まるまでクランプで固定している自作シャーシ
下写真が接着が完了した自作シャーシだ。
写真 接着が完了した自作シャーシ
下写真の水色は白アルミ複合板の保護シートだ。剥がすと白色アルミ複合板表面が露出する。
写真 自作シャーシの底板(アルミ複合板)
完成した自作シャーシの紹介
無事に完成した自作シャーシを写真で紹介しよう。
写真 リアパネルにはキャノンコネクタなど取り付ける
上写真はリアパネル。
ここにはキャノンコネクタを取り付ける予定だ。
具体的には左から順に以下を予定している。
XLR5オス | XLR5メス | XLR5メス | XLR5メス | USB-DAC |
![]() ![]() |
![]() ![]() |
![]() ![]() |
![]() ![]() |
![]() ![]() |
バランス出力 | バランス入力4 | バランス入力3 | バランス入力2 | バランス入力1 |
ただし、キャノンコネクタは一個千円くらいと高いので、四つの入力部分は当面は二つしか付けない。つまりUSB-DAC1とバランス入力2のみ。
USB-DACは以前に製作したぺるけ式秋月USB-DACのタムラトランスバージョン(下写真)をバランス出力に改造して、当アンプの入力1に組み込む予定なのだ。
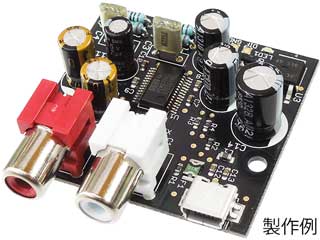
なおサイドウッド部分は木製なので、オール金属製のシャーシと比較すると静電シールド効果が劣るかも知れない。
なので、例えばアルミか銅のテープをシャーシ内部の木製部分に貼り付けるなどすると良いかも知れない。
写真 フロントにはバランスヘッドホン端子、入力切替プッシュボタン、ボリュームなど付ける
下写真はリアパネルにヒューズホルダー、ACメガネインレット、ACアウトレットを取り付けた状態だ。
写真 リアパネルにヒューズホルダー、ACメガネインレット、ACアウトレットを取り付けた
上写真のように市販のヒューズホルダー(Sato Parts F95-N)やACインレットなどがピッタリと加工済穴に収まるのは快感だ。
金属加工をハンドニブラや金工ヤスリを使って自分で加工すると言うのも電子工作の一部と考える事も出来る。
昔はワテもそんな金属加工をやっていたのだが、どんなに丁寧にシャーシ加工をやっても完成度の高い物を作るのは難しい。
それに、パネルに文字を入れるとなるとインスタントレタリングとか、透明テープに印刷して貼るなどの手段があるが、手間が掛かる。それにインスタントレタリングでは希望するフォントが入手出来ない場合もある。
かといって、自分で卓上CNCとか卓上レーザー加工機を使って文字の刻印をするとなると、かなり大掛かりなので導入には躊躇する。
そう言う問題を解決してくれるのがPCBWayさんのような加工業者さんだ。
フロントパネルのバランスヘッドホン出力端子はXLR5メスにする
さて、ぺるけ式FET差動バランス型ヘッドホンアンプにはバランス配線化したヘッドホンを接続する。
ワテ所有のオーディオテクニカのヘッドホンも配線は自分で改造してバランス化している。ただしコネクタ部分はアンバランスな普通のヘッドホンプラグを付けているので現状はアンバランス配線のままであるが(下記事参照)。
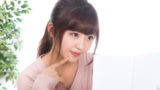
このヘッドホンにXLR5タイプのキャノンコネクタを付けてバランス接続を可能にするのだ。
一方、ヘッドホンアンプのフロントパネルにもXLR5コネクタを付けるのだ。
そこで問題になるのが、オス・メスどっちのコネクタをフロントパネルに取り付けるかと言う点だ。
通常のオーディオ機器はオス出しメス受けが基本なので、下写真のようにXLR5オスを使うのが普通だろう。
![]() |
![]() |
写真 XLR5オスコネクタ(Neutrik Dシリーズ)の取り付け例
ちなみに上写真右のようにシャーシ内部から取り付けると、見た目がスッキリする。
これもPCBWayさんのような専門業者さんにパネル加工を依頼するメリットの一つだろう。
もし自分でタケノコドリルを使ってΦ24の大穴を開けたとしても、こんなに綺麗な真円は開けられないからだ。
と言う訳で、最終的には下写真のようにXLR5メスコネクタを取り付ける事にした。
写真 バランスヘッドホン出力端子はXLR5メスに決めた
本来は出力端子はオスにすべきだがメスにした理由は、オスだとピンが出ていてそれがフロントパネルに来るのが何となく嫌なので。
それに市販のバランスヘッドホンアンプを見ても、何故だか出力端子にはXLRのオスを採用しているものが多いようなので。理由は知らない。
なお、XLR3を使う場合には左右チャンネルあるので二個必要になる。
XLR4やXLR5を使う場合には、一個有れば左右チャンネルを扱えるので一個で良い。
ワテの場合はジャンク屋で安売りしていたXLR5コネクタが沢山あるので、XLR5を採用した。
リアパネルのキャノンコネクタ取り付け穴加工にミスが発覚
さて、フロントパネルにはいい感じでXLR5メスコネクタを固定出来たのだが、リアパネルに大きな問題が有る事が発覚した。
写真 リアパネルにNeutrik DLシリーズコネクタがネジ止め出来ない問題発見
その問題とは、下写真のようにリアパネルにNeutrik DLシリーズコネクタがネジ止め出来ないのだ。
写真 ネジ穴位置が逆になってしまった(正しい位置に鉛筆で〇を書いた)
上写真を見ると分かるように、Neutrik DLシリーズコネクタの長方形フランジ部分にはΦ3.1の穴が二個開いている。
ところがその位置が逆だった!
なぜ取り付けネジ穴が逆になったのか?
当初はワテが用意したCADデータに間違いが有ったのかと思ったがそうではなかった。
ネジ穴が逆になった原因はワテが準備したシルク印刷用画像(下写真)にあったのだ。
つまり、下図のシルク文字印刷用PNG画像を
図 リアパネルのシルク印刷用データ(PNG画像)
下図のアルミ穴開け加工用CADデータに重ねてシルク印刷してもらうように指定していた。
図 リアパネル穴開け加工用CADデータ(STEP形式)
ところが、下図のようにリアパネルを上下逆にひっくり返して裏側にシルク印刷画像を重ねるとネジ穴位置が逆になってしまうのだ。
画像 リアパネル裏側から見た図
なぜこの問題が起こったのか?
それは本来なら下図に示すようにシルク印刷用のデータには文字だけでなく穴開け加工の輪郭線も入れておくべきだったのだ。
図 リアパネル穴開け加工3Dデータとシルク印刷用データ(文字と輪郭)を重ねた図
上図の水色で示す文字データと輪郭線データを一緒にまとめてPNG画像に変換してシルク印刷データとしてPCBWayさんにアップロードしておけば、今回の問題は起こらなかった。
つまり、この水色データに穴開け加工済アルミ板を重ねた場合、もしアルミ板を裏返しに重ねるとACインレットの辺りの形状が正しく重ならないからアルミ板の向きが違う事に気付くからだ。
つまりワテのミスなのだ。あかんがな。
ちなみに下図はフロントパネルのシルク印刷用にアップロードしたPNG画像だ。
図 フロントパネルのシルク印刷用データ(PNG画像)
この場合も、上図のように文字データのみで、ボリューム軸用Φ8mm丸穴や電源スイッチ(ロッカースイッチ)取り付け角穴、四連プッシュボタン取り付け丸穴などの輪郭形状は入れていなかった。でも幸い、フロントパネルは裏返しになる事は無かった。
恐らくその理由は「VOLUME」文字やその周囲にある円周上の目盛の点があるので、アルミ板に開いているΦ8mmの穴がその中心に来るのが分かるから、PCBWayのエンジニアの人がそれに気づいて正しい向きでシルク印刷してくれたのだと思う。
シルク印刷用データ作成の注意事項
と言う訳で、ワテと同じミスをしないようにするにはどうすれば良いだろうか?
幾つかの案が浮かぶので以下にまとめておこう。
- シルク印刷用データには文字データだけでなく穴開け加工の輪郭形状も入れておく
- シルク印刷用データが文字データだけの場合には、それをCADデータに重ねた図面も一緒に添付しておく
などが良いだろう。
ただし、方式1.のように、文字データと穴開け加工用輪郭データもミックスすると、そのデータが単純にシルク印刷に使われてしまうとアルミ板には文字だけでなく輪郭形状も印刷されてしまう可能性もある。
まあそんな単純ミスは起こらないとは思うが、もしそれを回避したいなら方式2.が良いだろう。
つまり下図のように三種類のデータをPCBWayさんにアップロードしておけば間違いない。
![]() |
![]() |
![]() |
CADデータ(STEP形式など) | シルク印刷データ(PNG,SVRなど) | 両者を重ねた図面 |
図 アルミ板の穴開け加工、シルク印刷加工で用意すると良い三つのデータ
今回の発注では、
- CADデータ(STEP形式など)
- シルク印刷データ(PNG,SVRなど)
の二つしかPCBWayさんに提供していなかったので、混乱が生じたのだ。
リアパネルにキャノンコネクタ取り付け穴を自分で開ける
さて、リアパネルのキャノンコネクタ取り付け穴位置が逆転してしまった問題を自力で解決する事にした。
まあ要するに穴を開け直せば良いのだ。単純な話だ。
ただし、リアパネル、フロントパネルは既にサイドウッドや底板に接着剤で貼り付けて箱状のシャーシになっているので、ワテ所有のアシナのボール盤のステージに載せて穴開け加工を行う事が出来ない。
そこで下写真に示すハンドグラインダーを使って穴開けを行う事にした。
写真 HiKOKI(日立工機) 電子ハンドグラインダ GP2VにΦ3mm鉄工ドリルを付けた
このHiKOKIのハンドグラインダはΦ3とΦ6の軸径の砥石を固定できるコレットチャックが付いている。
そこでΦ3mmの鉄工ドリルが上手く取り付けられたのでそれを使って下写真のようにΦ3の穴を開けた。
写真 リアパネルにΦ3の穴を開けている途中
ちなみにこのHiKOKIのハンドグラインダGP2Vは以前にハードオフで買っていたのだ。
さて、Φ3は開ける事が出来たのだが、NEUTRIK DLシリーズのXLRコネクタのフランジ固定用穴径はΦ3.1が推奨だ。手作業で開けた現状のΦ3穴だと、位置の誤差が大きくて多分M3ネジが引っ掛かって上手く嵌らないだろう。
そこで穴をΦ3.2に広げる事にした。
で、よく考えたら下写真のDREMEL MultiPro Variable speed ルーターの中古も持っていた。
写真 DREMEL MultiPro Variable speed ルーターの中古
最近、中古工具を良く買うので、上写真のHiKOKIは買ったのを覚えていたのだがこのDREMELのルーターは買った事すら忘れていた。
あかんがな。ボケとるがな。
これも中古で買った物だ。2000円くらいだったかな。速度可変なのだが、何故か低速域にすると回らないのだ。なので中速から高速域なら使える。
さらにこのルーターには付属品が多数あり、下写真のようにコレットチャックだけでなく、小型のドリルチャックも付いているだ。
写真 DREMEL MultiPro Variable speed ルーター付属ドリルチャックにΦ3.2を付けた
上写真のようにその小型ドリルチャックにΦ3.2鉄工ドリルを取り付けた。
そして、下写真のようにシャーシを固定しておいて、手作業でΦ3穴をΦ3.2に広げた。
写真 電動工具を使う時には対象物をしっかりクランプするのが基本だ
その結果、下写真のようにΦ3.2の穴開けに成功した。
写真 NEUTRIK DLシリーズXLRコネクタの取り付け穴開けに成功
そして、下写真のようにNEUTRIK DLシリーズの各種XLRコネクタをM3ネジで固定する事が出来た。
写真 PCBWay製アルミパネルにNEUTRIK XLRコネクタを内側から固定
この場合も、XLRコネクタはシャーシ内側から固定してみた。その方が見た目がスッキリするので。実際、上写真のように非常に綺麗に仕上がっている。
こう言う完成度の高い作品を作る事が出来るのも、加工業者さんに金属加工を発注する大きなメリットと言えるだろう。
下写真にはシャーシ内部から見たパネルの様子を紹介しよう。
写真 リアパネルに取り付けた各種のコネクタ(内側から)
写真 フロントパネルに取り付けたNEUTRIK XLR5コネクタ(内側から)
下写真が全体を撮影したものだ。
写真 PCBWay製アルミパネルで自作した「ぺるけ式FET差動バランス型ヘッドホンアンプ」用シャーシ
と言う訳で、鮮やかなオレンジ色っぽいパネル、ウオルナット色のサイドウッド、そしてNEUTRIK DLシリーズのXLRコネクタの組み合わせで、メーカー製のオーディオ機器のような完成度の高さを実現する事が出来たのだ。
アルミシャーシをハンドニブラや金工ヤスリで加工する手法では到底実現出来ない。
ボリューム、プリント基板などの取り付け準備
シャーシ、コネクタ取り付けが完了したので、残す作業はプリント基板の固定と配線作業だ。
ボリュームは3D印刷した台座に固定する
ぺるけ式FET差動バランス型ヘッドホンアンプには下写真のように四連ボリュームを使う。
写真 四連ボリュームは3Dプリンタで印刷した台座に固定する事にした
上写真のようにALPS製50KΩ四連ボリュームはパネルに直接固定するのではなく、3Dプリンタで印刷した台座に固定した。
その理由は、ボリュームをパネルに直接取り付けるとボリューム軸をカットする必要があるがそれが面倒なので。
それとこの3Dプリンタ製台座は以前に金田式DCプリアンプ製作時に印刷したのだが、設計ミスで穴位置を間違えていて廃棄予定だったのだが、次回作で使えるかも知れないと思って保管していたのだ。
それを今回、無事に活用出来たのだ。こう言うのもSDGs(エス・ディー・ジーズ)って言うのかな?
ぺるけ式秋月USB-DACタムラトランス版を組み込む
下写真は、確か十年くらい前に自作したぺるけ式秋月USB-DACタムラトランス版だ。
写真 十年くらい前に自作したぺるけ式秋月USB-DACタムラトランス版を組み込む
このUSB-DACを今回作成している「ぺるけ式FET差動バランス型ヘッドホンアンプ」の入力1番に組み込むのだ。
なおこのUSB-DAC出力はタムラTpAs-2Sを搭載しているが、現状ではその出力部分はアンバランス出力に成っている。
そこで、その出力部分をバランス出力に変更して、今回作成している「ぺるけ式FET差動バランス型ヘッドホンアンプ」の入力1番に組み込むのだ。
ちなみにアンバランス出力をバランス出力に変更すると言っても、大掛かりな改良は不要で、単にトランス出力部の配線を少し変更するだけで良い。
3D印刷した自作貼付スペーサーを使ってプリント基板を固定する
この記事で紹介したように、先日、3Dプリンタを使って貼付スペーサーを自作した。
裏側にはM3ナットを埋め込む構造だ。
写真 3Dプリンタで印刷した貼付スペーサー(20x20mm、高さ9mm)
下写真のように自作貼り付けスペーサーの裏側に強力な両面テープを貼る。
写真 自作貼付スペーサーとバランス型ヘッドホンアンプ用基板
これらの貼付スペーサーを下写真のようにプリント基板に取り付けた。
写真 自作貼付スペーサーをプリント基板に取り付けた
あとは基板の貼り付け場所を決めて貼り付ければよい。
オールPCBWay基板「ぺるけ式FET差動バランス型ヘッドホンアンプ」配線前
さて、いよいよ配線作業なのだが、今回は下写真に示すように七枚のプリント基板を使う。
写真 「ぺるけ式FET差動バランス型ヘッドホンアンプ」の七枚の基板
上写真の七枚の基板のうち、タムラトランスが載っている緑基板はマザーツール製ユニバーサル基板だが、残り六枚は全てPCBWayさん発注の両面スルーホールガラスエポキシ1.6ミリ厚基板なのだ。
と言う訳で、自作オーディオの世界には
〇〇式オールメタルキャントランジスタパワーアンプ
などの製作例があるが、今回ワテが作成しているアンプは
と言う事になるのだ。
長いわ。
まあオーディオマニアな人は、アンプに使われている素子や配線材料の違いで音の違いが分かるそうだが、もっと上級マニアになるとプリント基板のメーカーの違いですら聞き分ける事が出来るのかも知れない。
あるいは同じPCBWay製基板でも赤色レジスト基板の音は情熱的な音だ!とか、白色レジスト基板の音は色付けの無いナチュラルな音だ!とか、黒色レジスト基板の色は重厚感がある!などと聞き分けられるのかも知れない。
まさに見たまんま!
と言う事で、配線作業はかなり手間が掛かりそうなので次回記事で紹介したい。
PCBWay製アルミパネルで製作した自作シャーシの紹介
以下では、今回作成したシャーシの全体写真を紹介しよう。
写真 フロントパネルにはTRSヘッドホン端子(アンバランス)、XLR5メス(バランス)を取り付けた
写真 リアパネルにはXLR5オス(出力)、XLR5メス(BAL入力2)、USB-DAC1など付けた
写真 アルミ複合板採用の天板、底板(297x210x3t)は手軽で便利
まとめ

ワレコ
いや~、疲れた。
配線作業は次回記事で紹介したい。
当記事では、PCBWayさんに発注していたアルミパネルを利用して自作したシャーシの製作過程を紹介した。
二枚のアルミパネルに穴開け加工、アルマイト加工、シルク印刷を依頼して約140ドル。日本円なら17,000円弱だ。日本の業者さんに類似の加工を依頼すると、恐らく最低でも二倍から三倍以上の費用が掛かるだろう。
ハンドニブラや金工ヤスリを使ってアルミシャーシを手作業で加工している人には金属加工の外注を是非お勧めしたい。
と言う事で、
「ワレコ式オールPCBWay基板採用ぺるけ式FET差動バランス型ヘッドホンアンプ15Vバージョン with ぺるけ式秋月USB-DACタムラトランスTpAs-2S版」
の配線作業にこれから取り掛かる。
その詳細は次回記事で紹介したい。
(続く)
コメント